Method for improving spacer shape
An isolation sidewall and isolation sidewall etching technology, applied in electrical components, semiconductor/solid-state device manufacturing, circuits, etc., can solve problems such as poly damage, achieve straight morphology, and increase the etching selectivity ratio.
- Summary
- Abstract
- Description
- Claims
- Application Information
AI Technical Summary
Problems solved by technology
Method used
Image
Examples
no. 1 example
[0028] Such as figure 2 As shown, the present invention provides a first embodiment of a method for improving the morphology of isolation spacers in the production of semiconductor devices, including:
[0029] 1) Deposit the isolation side wall film;
[0030] 2) Perform plasma anisotropic bombardment, the angle of the plasma anisotropic bombardment is vertical bombardment from the top of the device to the bottom, refer to image 3 shown;
[0031] 3) Depositing the isolation side wall film again;
[0032] 4) Then perform isolation spacer etching.
[0033] Wherein, the spacer film is a nitride film, and the plasma is nitrogen, chlorine, hydrogen chloride, bromine or hydrogen bromide.
no. 2 example
[0034] The present invention provides a second embodiment of a method for improving the morphology of isolation sidewalls in the production of semiconductor devices, including:
[0035] 1) Deposit the isolation side wall film;
[0036] 2) Perform plasma anisotropic bombardment, the angle of the plasma anisotropic bombardment is vertical bombardment from the top of the device to the bottom, refer to image 3 shown;
[0037] Wherein, the plasma anisotropic bombardment pressure is 5mt-10mt, preferably 6mt, 7mt, 8mt or 9mt.
[0038] The power of the plasma anisotropic bombardment source is 400W-700W, preferably 500W or 600W.
[0039] The plasma anisotropic bombardment bias voltage is 100V-200V, preferably 150V.
[0040] 3) Depositing the isolation side wall film again;
[0041] 4) Then perform isolation spacer etching.
[0042] Wherein, the spacer film is a nitride film.
no. 3 example
[0043] The present invention provides a third embodiment of a method for improving the morphology of isolation sidewalls in the production of semiconductor devices, including:
[0044] 1) Depositing an isolation spacer film; the isolation spacer film is a nitride film.
[0045] 2) Perform plasma anisotropic bombardment, the angle of the plasma anisotropic bombardment is vertical bombardment from the top of the device to the bottom, refer to image 3 shown;
[0046] Wherein, the plasma is nitrogen, chlorine, hydrogen chloride, bromine or hydrogen bromide.
[0047] The plasma anisotropic bombardment pressure is 5mt-10mt, preferably 6mt, 7mt, 8mt or 9mt.
[0048] The power of the plasma anisotropic bombardment source is 400W-700W, preferably 500W or 600W.
[0049] The plasma anisotropic bombardment bias voltage is 100V-200V, preferably 150V.
[0050] 3) Depositing the isolation side wall film again;
[0051] 4) Then perform isolation sidewall etching;
[0052] The etching g...
PUM
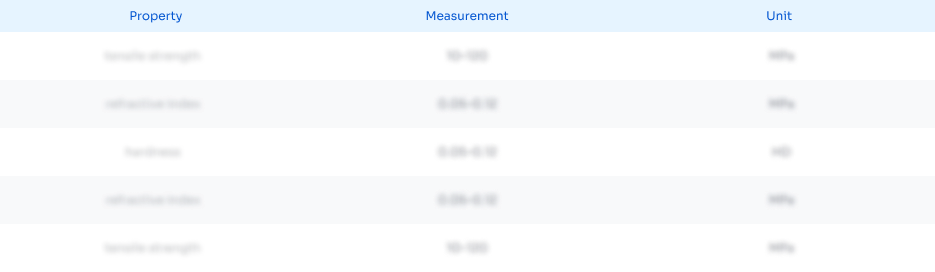
Abstract
Description
Claims
Application Information

- R&D Engineer
- R&D Manager
- IP Professional
- Industry Leading Data Capabilities
- Powerful AI technology
- Patent DNA Extraction
Browse by: Latest US Patents, China's latest patents, Technical Efficacy Thesaurus, Application Domain, Technology Topic, Popular Technical Reports.
© 2024 PatSnap. All rights reserved.Legal|Privacy policy|Modern Slavery Act Transparency Statement|Sitemap|About US| Contact US: help@patsnap.com