Method and system for recovering ammonia from byproduct ammonium chloride of potassium nitrate technology
A technology of potassium nitrate and ammonium chloride, applied in the field of chemical technology, can solve the problems of large desiccant, high energy consumption, cumbersome process flow of ammonia gas recovery process, etc., and achieve the effects of reducing consumption, reducing consumption and simple process
- Summary
- Abstract
- Description
- Claims
- Application Information
AI Technical Summary
Problems solved by technology
Method used
Image
Examples
Embodiment 1
[0041] The atmospheric pressure of the place where the implementation case is located is 73KPaA.
[0042] After dissolving the wet ammonium chloride produced in the potassium nitrate process, 80kg / h of ammonium chloride solution containing 15wt% ammonium chloride at 25°C (the net ammonia content is about 3.81kg / h) is sent into the heat exchange system and steamed with ammonia The ammonia-containing gas discharged from the top of the tower is exchanged for heat. After the heat exchange, the ammonium chloride solution is 73°C, and the ammonia-containing gas at the top of the tower is cooled from 78°C to 57.3°C. The ammonium chloride solution after heat exchange is sent to the top of the ammonia distillation tower, and at the same time, 29kg / h of milk of lime containing 200tt active CaO at 85°C is added to the pre-ash bucket, and 13kg of fresh saturated steam of 0.5MPaG is fed into the bottom of the ammonia distillation tower / h. Control the operating pressure at the top of the ...
Embodiment 2
[0053] The atmospheric pressure of the place where the implementation case is located is 73KPaA.
[0054] After dissolving the wet ammonium chloride produced in the potassium nitrate process, 50kg / h of ammonium chloride solution containing 17wt% ammonium chloride at 25°C (the net ammonia content is about 2.70kg / h) is sent into the heat exchange system to be steamed with ammonia The ammonia-containing gas discharged from the top of the tower is exchanged for heat. After the heat exchange, the ammonium chloride solution is 50°C, and the ammonia-containing gas at the top of the tower is cooled from 71.3°C to 62.3°C. The ammonium chloride solution after heat exchange is sent to the top of the ammonia distillation tower, and at the same time, 24.8kg / h of lime milk containing 160tt active CaO at 85°C is added to the pre-ash bucket, and fresh saturated steam of 0.2MPaG is fed into the bottom of the ammonia distillation tower 10kg / h. Control tower top operating pressure -0.01MPaG.
...
Embodiment 3
[0065] The atmospheric pressure of the place where the implementation case is located is 73KPaA.
[0066] After dissolving the wet ammonium chloride produced in the potassium nitrate process, 50kg / h of ammonium chloride solution containing 17wt% ammonium chloride at 25°C (the net ammonia content is about 2.70kg / h) is sent into the heat exchange system to be steamed with ammonia The ammonia-containing gas discharged from the top of the tower is exchanged for heat. After the heat exchange, the ammonium chloride solution is 70°C, and the ammonia-containing gas at the top of the tower is cooled from 80.6°C to 66.8°C. The ammonium chloride solution after heat exchange is sent to the top of the ammonia distillation tower, and at the same time, 28.4kg / h of milk of lime containing 140tt active CaO at 85°C is added to the pre-ash bucket, and 0.1MPaG fresh saturated steam is fed into the bottom of the ammonia distillation tower 11kg / h. Control the operating pressure at the top of the t...
PUM
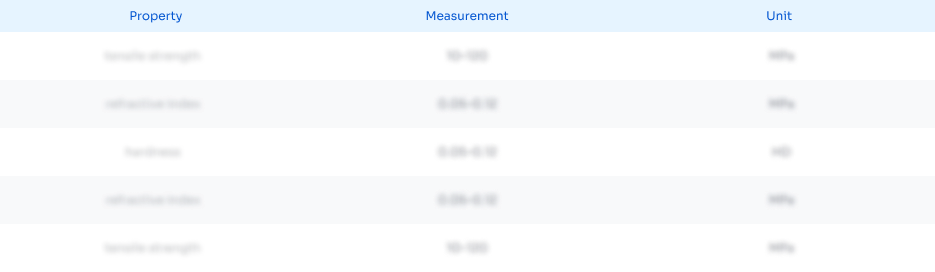
Abstract
Description
Claims
Application Information

- R&D
- Intellectual Property
- Life Sciences
- Materials
- Tech Scout
- Unparalleled Data Quality
- Higher Quality Content
- 60% Fewer Hallucinations
Browse by: Latest US Patents, China's latest patents, Technical Efficacy Thesaurus, Application Domain, Technology Topic, Popular Technical Reports.
© 2025 PatSnap. All rights reserved.Legal|Privacy policy|Modern Slavery Act Transparency Statement|Sitemap|About US| Contact US: help@patsnap.com