Preparation method of Fe/N/C codoped electrocatalyst for efficient oxygen reduction reaction and application of Fe/N/C codoped electrocatalyst for efficient oxygen reduction reaction
An electrocatalyst and co-doping technology, applied in the field of electrocatalysis, can solve problems such as complex preparation methods, and achieve the effects of simple preparation process, improved electrical conductivity, and favorable adsorption and desorption.
- Summary
- Abstract
- Description
- Claims
- Application Information
AI Technical Summary
Problems solved by technology
Method used
Image
Examples
Embodiment 1
[0031] (1) Dissolve 40 mg of pretreated carbon black, 1.60 g of glucose, and 20 mg of sodium dodecylsulfonate into 20 ml of secondary water, sonicate for 4 h to form a uniform black suspension, and then add 0.5 mmol Ferric nitrate, transfer the solution to a hydrothermal reaction kettle, set the oven temperature to 180 °C, and the reaction time is 15 h, naturally cool to room temperature, filter with suction, wash with secondary water three times, dry in a vacuum oven at 60 °C, fully A black powder was obtained after grinding.
[0032](2) Take 80 mg of black powder sample (intermediate product) and 800 mg of melamine and mix them thoroughly and place them in a tube furnace with a mass ratio of 1:10. Pyrolyze at high temperature under nitrogen atmosphere, and the pyrolysis temperature is 900 ℃, time 1 h, heating rate 10 ℃ / min, to obtain a black solid powder, denoted as Fe 0.5 NC-900-2.
Embodiment 2
[0034] (1) Dissolve 40 mg of pretreated carbon black, 1.60 g of glucose, and 20 mg of sodium dodecylsulfonate into 20 ml of secondary water, sonicate for 4 h to form a uniform black suspension, and then add 1.5 mmol Ferric nitrate, transfer the solution to a hydrothermal reaction kettle, set the oven temperature to 180 °C, and the reaction time is 15 h, naturally cool to room temperature, filter with suction, wash with secondary water three times, dry in a vacuum oven at 60 °C, fully A black powder was obtained after grinding.
[0035] (2) Take 80 mg of black powder sample (intermediate product) and 800 mg of melamine and mix them thoroughly and place them in a tube furnace with a mass ratio of 1:10. Pyrolyze at high temperature under nitrogen atmosphere, and the pyrolysis temperature is 900 ℃, time 1 h, heating rate 10 ℃ / min, to obtain a black solid powder, denoted as Fe 1.5 NC-900-2.
Embodiment 3
[0037] (1) Dissolve 40 mg of pretreated carbon black, 1.60 g of glucose, and 20 mg of sodium dodecylsulfonate into 20 ml of secondary water, sonicate for 4 h to form a uniform black suspension, and then add 2.5 mmol Ferric nitrate, transfer the solution to a hydrothermal reaction kettle, set the oven temperature to 180 °C, and the reaction time is 15 h, naturally cool to room temperature, filter with suction, wash with secondary water three times, dry in a vacuum oven at 60 °C, fully A black powder was obtained after grinding.
[0038] (2) Take 80 mg of black powder sample (intermediate product) and 800 mg of melamine and mix them thoroughly and place them in a tube furnace with a mass ratio of 1:10. Pyrolyze at high temperature under nitrogen atmosphere, and the pyrolysis temperature is 900 ℃, time 1 h, heating rate 10 ℃ / min, to obtain a black solid powder, denoted as Fe 2.5 NC-900-2.
PUM
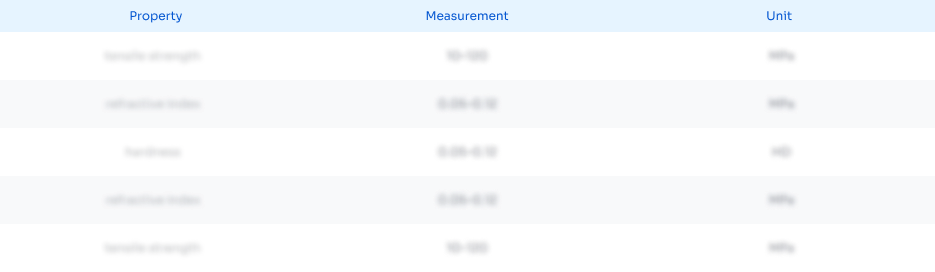
Abstract
Description
Claims
Application Information

- Generate Ideas
- Intellectual Property
- Life Sciences
- Materials
- Tech Scout
- Unparalleled Data Quality
- Higher Quality Content
- 60% Fewer Hallucinations
Browse by: Latest US Patents, China's latest patents, Technical Efficacy Thesaurus, Application Domain, Technology Topic, Popular Technical Reports.
© 2025 PatSnap. All rights reserved.Legal|Privacy policy|Modern Slavery Act Transparency Statement|Sitemap|About US| Contact US: help@patsnap.com