Plate-fin type heat exchanger core and fin structure thereof
A heat exchanger, plate-fin type technology, applied in the field of plate-fin heat exchanger core body, can solve the problems of weakening the strength of plate-fin heat exchanger, reducing the pressure resistance capacity of plate-fin structure, and not significantly improving heat transfer performance , to achieve the effect of improving the overall heat transfer efficiency, improving the local enhanced heat transfer coefficient, and improving the problem of insufficient strength
- Summary
- Abstract
- Description
- Claims
- Application Information
AI Technical Summary
Problems solved by technology
Method used
Image
Examples
Embodiment approach
[0050] see Figure 1 to Figure 2 As shown, the present invention provides a core body of a plate-fin heat exchanger, comprising several partitions (1, 6), fins 100 and seals 7, and two corresponding partitions (1, 6) between the fins 100 ) support, adjacent partitions (1, 6) are sealed by seals 7 to form hot runner 4 / cold runner 5 between adjacent partitions, and several runners are stacked and connected by diffusion welding or brazing , forming a plate-fin heat exchanger core, which can form flow forms such as forward flow, countercurrent flow, and cross flow, and can realize multi-flow flow.
[0051] see Figure 3 to Figure 9 As shown, it is a schematic structural diagram of the fin 100 of the plate-fin heat exchanger; the fin 100 is mainly composed of a punched spherical convex 2 / spherical concave 3 flow channel, and the punched hole 200 includes no offset and offset There are two types of structure a, and the spherical convex / spherical concave structures on both sides of...
PUM
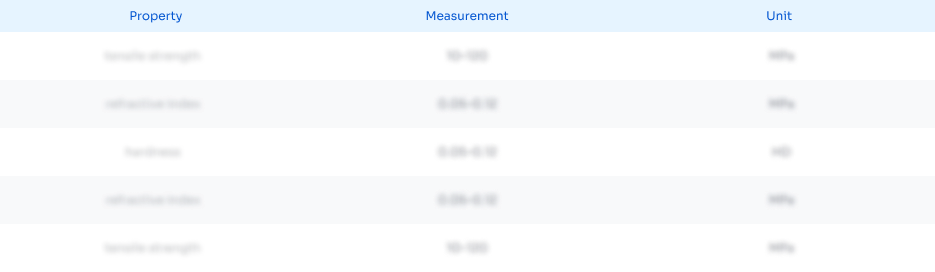
Abstract
Description
Claims
Application Information

- R&D
- Intellectual Property
- Life Sciences
- Materials
- Tech Scout
- Unparalleled Data Quality
- Higher Quality Content
- 60% Fewer Hallucinations
Browse by: Latest US Patents, China's latest patents, Technical Efficacy Thesaurus, Application Domain, Technology Topic, Popular Technical Reports.
© 2025 PatSnap. All rights reserved.Legal|Privacy policy|Modern Slavery Act Transparency Statement|Sitemap|About US| Contact US: help@patsnap.com