Method for protecting ultrasonic probe
An ultrasonic and metal melt technology, applied in the field of material liquid processing, can solve the problems of poor processing effect, reduced energy, large acoustic impedance value of niobium alloy, etc., and achieve the effects of increasing agitation, reducing secondary oxidation, and simple equipment
- Summary
- Abstract
- Description
- Claims
- Application Information
AI Technical Summary
Problems solved by technology
Method used
Image
Examples
Embodiment 1
[0066] A. Alloy raw material configuration and smelting: put 0.36kg of industrially pure aluminum with a purity of 99.7% and 0.016kg of an aluminum-silicon master alloy with a silicon content of 24.4% into a melting furnace, and melt it into Al after 30 minutes -1%Si (the percentages used in the present invention are percentages by weight, the same below) melt 0.38kg, and overheated by 10°C;
[0067] B. Molten salt powder configuration and melting: take 32g of chemically pure reagent LiCl and CaCl 2 Get 18g according to (64%LiCl+36%CaCl 2 ) and mixed evenly, a total of 50g, heated and melted for 20 minutes to make it in a molten state, overheated to 80°C, and set aside for later use;
[0068] C, pour molten salt: the Al-1%Si melt that does not obtain step is poured in the crucible, then melted (64%LiCl+36%CaCl 2 ) The mixed molten salt is poured over the Al-1%Si melt, so that the molten salt maintains a height of 15mm above the melt;
[0069] D. Ultrasonic probe immersed in...
Embodiment 2
[0074] A. Alloy raw material configuration and smelting: Take 1kg of industrial pure aluminum with a purity of 99.7% and 0.14kg of an aluminum-silicon master alloy with a purity of 20% as a furnace charge, and put them in a melting furnace for 60 minutes to melt into Al- 2.5% Si melt, and superheated at 60°C;
[0075]B, molten salt powder configuration and melting: each get chemically pure reagent LiCl to be 80g, CaCl to be 40g, KCl to be 80g, pulverize and grind, and according to the ratio (40%LiCl+20%CaCl 2 +40%KCl) mixed evenly, 200g in total; after heating for 50 minutes, make it into a molten state, overheat at 45°C, and put it aside for later use;
[0076] C, pour molten salt: the Al-2.5%Si melt that step A obtains is poured in the crucible, then melted (40%LiCl+20%CaCl 2 +40% KCl) mixed molten salt is poured over the Al-2.5% Si melt, so that the molten salt maintains a height of 90 mm above the melt;
[0077] D. Ultrasonic probe immersed in molten salt: immerse the ul...
Embodiment 3
[0082] A. Alloy raw material configuration and smelting: 120kg of cast pig iron with the brand name Q12, 21.96kg of scrap steel with a carbon content of 0.2%, and 1.5kg of ferrosilicon with a silicon content of 75% are used as raw materials to prepare 144kg of gray cast iron, and the prepared The raw materials were put into a 200kW thyristor-controlled induction furnace, and after 90 minutes, the cast iron melt was melted and overheated at 100°C; the nominal composition of the gray cast iron prepared was as follows (the stated alloy compositions are all mass percentages, the same below ): C=3.5%; Si=1.8%; Mn=0.2%; S<0.03%; P<0.07%. Carbon equivalent = 4.1, close to eutectic composition cast iron.
[0083] B, molten salt powder configuration and melting: each get chemically pure reagent NaCl to be 200g, KCl to be 200g, AlF to be 100g, pulverize and grind, and according to the ratio (40%NaCl+40%KCl+20%AlF 3 ) mixed evenly, 500g in total; after heating for 90 minutes, it was in ...
PUM
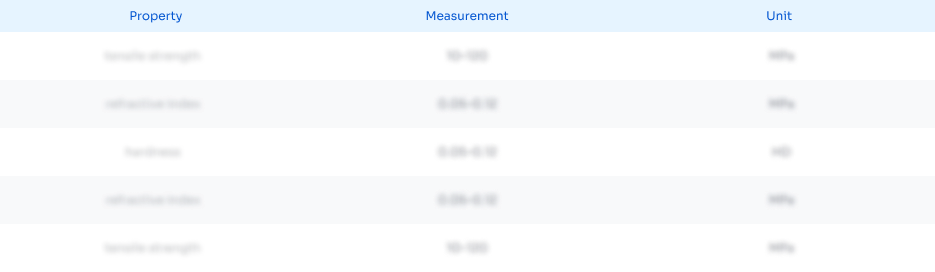
Abstract
Description
Claims
Application Information

- R&D
- Intellectual Property
- Life Sciences
- Materials
- Tech Scout
- Unparalleled Data Quality
- Higher Quality Content
- 60% Fewer Hallucinations
Browse by: Latest US Patents, China's latest patents, Technical Efficacy Thesaurus, Application Domain, Technology Topic, Popular Technical Reports.
© 2025 PatSnap. All rights reserved.Legal|Privacy policy|Modern Slavery Act Transparency Statement|Sitemap|About US| Contact US: help@patsnap.com