Preparation method of polyethylene/graphene master batch
A polyethylene and graphene technology, applied in the field of preparation of polyethylene/graphene master batches, can solve problems such as large environmental hazards, unfavorable re-dispersion, etc., and achieve the effects of low cost, green and pollution-free preparation process, and simple process
- Summary
- Abstract
- Description
- Claims
- Application Information
AI Technical Summary
Problems solved by technology
Method used
Image
Examples
Embodiment 1
[0028] (1) 1g of graphite oxide was added to 200g of water, stirred at 100rpm and 20°C for 0.5h, then ultrasonicated at 500W and 60°C for 30min to disperse and exfoliate to obtain a graphene oxide aqueous solution;
[0029] Add 50% aqueous polyethylene wax emulsion containing 1g of polyethylene into the graphene oxide aqueous solution, stir and mix evenly, then add 2g of 10% calcium chloride solution for demulsification, and obtain polyethylene / graphene oxide particle suspension ;
[0030] (2) Add 5g of vitamin C to the polyethylene / graphene oxide particle suspension prepared in step (1), reduce it for 10 hours at 80°C, and filter it under a vacuum with a vacuum degree of 0.01MPa and a temperature of 60°C. After drying in an oven for 24 hours, the polyethylene / graphene master batch with a graphene content of 50% was obtained.
Embodiment 2
[0032] (1) 1g of graphite oxide was added to 100g of water, stirred at 200rpm and 40°C for 2h, then ultrasonicated at 100W and 80°C for 60min to disperse and peel off to obtain a graphene oxide aqueous solution,
[0033] Add 45% aqueous polyethylene wax emulsion containing 1.5g polyethylene into the graphene oxide aqueous solution, stir and mix evenly, then add 5g 15% magnesium chloride solution for demulsification, and obtain polyethylene / graphene oxide particle suspension;
[0034] (2) Add 10 g of vitamin C to the polyethylene / graphene oxide particle suspension prepared in step (1), reduce it for 24 hours at 25° C. After drying in an oven for 24 hours, a polyethylene / graphene master batch with a graphene content of 40% was obtained.
Embodiment 3
[0036] (1) 1g of graphite oxide was added to 100g of water, stirred at 300rpm and 30°C for 1h, then ultrasonicated at 300W and 40°C for 10min to disperse and peel off to obtain a graphene oxide aqueous solution,
[0037] Add 30% aqueous polyethylene wax emulsion containing 2.3g of polyethylene into the graphene oxide aqueous solution, stir and mix evenly, then add 1g of 10% aluminum chloride solution for demulsification, and obtain polyethylene / graphene oxide particle suspension liquid;
[0038] (2) Add 10 g of glucose to the polyethylene / graphene oxide particle suspension prepared in step (1), reduce it for 24 hours at 80°C, and filter it in a vacuum oven with a vacuum of 0.07MPa and a temperature of 70°C After drying for 15 hours in medium, a polyethylene / graphene masterbatch with a graphene content of 30.3% was obtained.
PUM
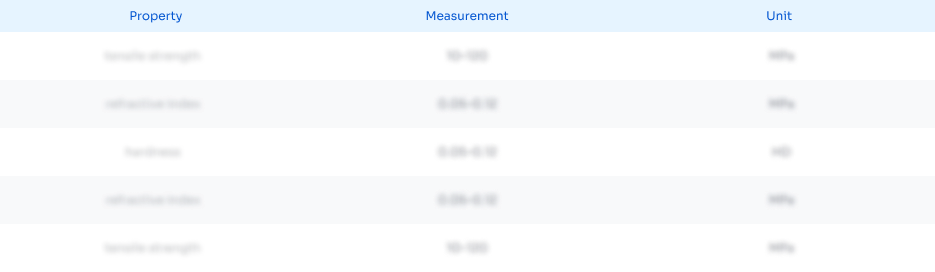
Abstract
Description
Claims
Application Information

- Generate Ideas
- Intellectual Property
- Life Sciences
- Materials
- Tech Scout
- Unparalleled Data Quality
- Higher Quality Content
- 60% Fewer Hallucinations
Browse by: Latest US Patents, China's latest patents, Technical Efficacy Thesaurus, Application Domain, Technology Topic, Popular Technical Reports.
© 2025 PatSnap. All rights reserved.Legal|Privacy policy|Modern Slavery Act Transparency Statement|Sitemap|About US| Contact US: help@patsnap.com