Anti-slip wood-plastic floor and production method
A technology of wood-plastic floor and production method, applied in the field of wood-plastic floor, can solve the problems of poor anti-skid performance, low wear coefficient and elastic coefficient of the floor, and achieve the advantages of easy popularization and promotion, low brittleness and high elongation. Effect
- Summary
- Abstract
- Description
- Claims
- Application Information
AI Technical Summary
Problems solved by technology
Method used
Image
Examples
Embodiment 1
[0049] Embodiment 1. The raw materials used in the manufacture of non-slip wood-plastic flooring are as follows in parts by weight:
[0050] 15-16 parts of resin, 13-14 parts of styrene-butadiene rubber, 30-40 parts of wood powder, 3-4 parts of silicon dioxide, 6-9 parts of epoxy resin, 15-20 parts of calcium carbonate, 5- 8 parts, 2-3 parts of coupling agent, 2-3 parts of other additives.
[0051] S1: Add styrene-butadiene rubber, resin, plasticizer oil and toughening agent into the melting furnace according to the above weight, and add other additives to melt at the same time;
[0052] S2: Then add silicon dioxide, epoxy resin, calcium carbonate, plasticizer oil and coupling agent into the melting furnace, stir at high speed for 15-20 minutes to granulate;
[0053] S3: Extrude the mixed raw material obtained in S2 through a twin-screw extruder, and the temperature of each zone of the extruder is:
[0054] Zone 1 temperature: 160~165℃,
[0055] Zone 2 temperature: 165~170℃...
Embodiment 2
[0063] Embodiment 2. The raw materials used in the manufacture of non-slip wood-plastic flooring are as follows in parts by weight:
[0064] 16-17 parts of resin, 14-15 parts of styrene-butadiene rubber, 30-40 parts of wood powder, 3-4 parts of silicon dioxide, 6-9 parts of epoxy resin, 15-20 parts of calcium carbonate, 5- 8 parts, 2-3 parts of coupling agent, 3 parts of toughening agent, 2-3 parts of other additives.
[0065] S1: Add styrene-butadiene rubber, resin, plasticizer oil and toughening agent into the melting furnace according to the above weight, and add other additives to melt at the same time;
[0066] S2: Then add silicon dioxide, epoxy resin, calcium carbonate, plasticizer oil and coupling agent into the melting furnace, stir at high speed for 15-20 minutes to granulate;
[0067] S3: Extrude the mixed raw material obtained in S2 through a twin-screw extruder, and the temperature of each zone of the extruder is:
[0068] Zone 1 temperature: 160~165℃,
[0069]...
Embodiment 3
[0077] Embodiment 3, the raw materials used in the manufacture of anti-skid type wood-plastic floor are as follows in parts by weight:
[0078] 16-17 parts of resin, 15-16 parts of styrene-butadiene rubber, 30-40 parts of wood powder, 3-4 parts of silicon dioxide, 6-9 parts of epoxy resin, 15-20 parts of calcium carbonate, 5- 8 parts, 2-3 parts of coupling agent, 3-4 parts of toughening agent, 2-3 parts of other additives.
[0079] S1: Add styrene-butadiene rubber, resin, plasticizer oil and toughening agent into the melting furnace according to the above weight, and add other additives to melt at the same time;
[0080] S2: Then add silicon dioxide, epoxy resin, calcium carbonate, plasticizer oil and coupling agent into the melting furnace, stir at high speed for 15-20 minutes to granulate;
[0081] S3: Extrude the mixed raw material obtained in S2 through a twin-screw extruder, and the temperature of each zone of the extruder is:
[0082] Zone 1 temperature: 160~165℃,
[...
PUM
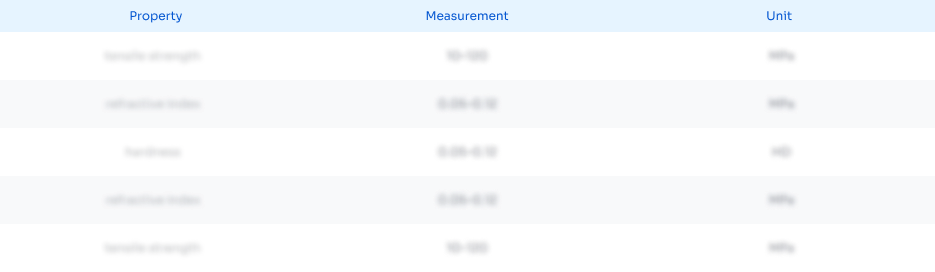
Abstract
Description
Claims
Application Information

- R&D Engineer
- R&D Manager
- IP Professional
- Industry Leading Data Capabilities
- Powerful AI technology
- Patent DNA Extraction
Browse by: Latest US Patents, China's latest patents, Technical Efficacy Thesaurus, Application Domain, Technology Topic, Popular Technical Reports.
© 2024 PatSnap. All rights reserved.Legal|Privacy policy|Modern Slavery Act Transparency Statement|Sitemap|About US| Contact US: help@patsnap.com