Preparation method of carbon tube coated magnetic material and magnetic oriented heat conduction material
A technology of magnetic materials and heat-conducting materials, which is applied in the preparation of carbon tube-coated magnetic materials and the field of magnetically oriented heat-conducting materials, which can solve the problem that the thermal conductivity does not exert the desired effect, the heat transfer efficiency of heat-conducting materials is low, and the magnetic properties of carbon nanotubes Instability and other problems, to achieve the effect of improving heat transfer efficiency, good heat transfer uniformity, and high magnetic stability
- Summary
- Abstract
- Description
- Claims
- Application Information
AI Technical Summary
Problems solved by technology
Method used
Image
Examples
preparation example Construction
[0027] The present invention firstly provides a kind of preparation method of carbon tube coating magnetic material, comprises the following steps:
[0028] Step S1, the cobalt source and 2-methylimidazole are respectively dissolved in methanol and mixed to obtain a mixed solution C. The mixed solution C is subjected to solid-liquid separation to obtain a precipitate, and the precipitate is dried to obtain the framework material ZIF-67;
[0029] In step S2, the framework material ZIF-67 is calcined for the first time under a mixed atmosphere of hydrogen and argon to obtain an intermediate material;
[0030] In step S3, the intermediate material is calcined for the second time under an air atmosphere to obtain a carbon tube-coated magnetic material.
[0031] According to the present invention, step S1 is first carried out to prepare the framework material ZIF-67; specifically, the cobalt source is dissolved in methanol to form solution A, and 2-methylimidazole is dissolved in m...
Embodiment 1
[0043] This embodiment provides a method for preparing a carbon tube-coated magnetic material, comprising the following steps:
[0044] Weigh 0.975g of 2-methylimidazole and 0.432g of cobalt nitrate hexahydrate and dissolve them in 30ml of methanol, add the solution of cobalt nitrate hexahydrate dropwise into the 2-methylimidazole solution under stirring conditions, continue stirring for 10min, and let it stand After 24 hours, the product after standing still was centrifuged and the lower layer solid was taken, namely ZIF-67;
[0045] 0.2g of ZIF-67 in H 2 with Ar(H 2 Calcined at 800°C for 2 hours in a mixed atmosphere with a volume ratio of 1:10 to Ar, and then calcined at 250°C for 6 hours in an air atmosphere to obtain a carbon tube-coated magnetic material.
[0046] The prepared carbon tube-coated magnetic material was detected by transmission electron microscopy, and the results were as follows: figure 1 shown by figure 1 It can be seen that the magnetic material is w...
Embodiment 2
[0048]This embodiment provides a method for preparing a magnetically oriented thermally conductive material, which includes the following steps:
[0049] Dope the carbon tube-coated magnetic material obtained in Example 1 into epoxy resin and curing agent to obtain a mixed solution D. In a solution state, place the mixed solution D in a magnetic field for 30 minutes, and then pre-cure at 100°C 1 hour, and then cured at 120° C. for 1 hour to obtain a magnetically oriented thermally conductive material.
[0050] Scanning electron microscopy was carried out on the prepared magnetically oriented thermally conductive material, and the results were as follows: figure 2 shown by figure 2 It can be seen that the morphology of C@Co / EP is uniform.
PUM
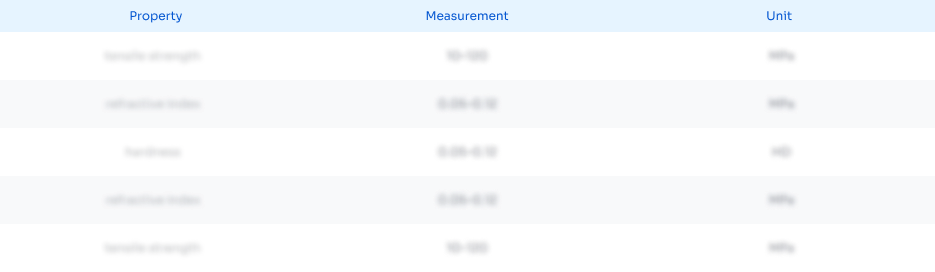
Abstract
Description
Claims
Application Information

- R&D Engineer
- R&D Manager
- IP Professional
- Industry Leading Data Capabilities
- Powerful AI technology
- Patent DNA Extraction
Browse by: Latest US Patents, China's latest patents, Technical Efficacy Thesaurus, Application Domain, Technology Topic, Popular Technical Reports.
© 2024 PatSnap. All rights reserved.Legal|Privacy policy|Modern Slavery Act Transparency Statement|Sitemap|About US| Contact US: help@patsnap.com