Display screen assembly, preparation method thereof and display terminal
A technology for display components and display screens, which can be used in instruments, identification devices, etc., to solve the problems of cracking, glass material selection not too thick, glass strength is not high, etc.
- Summary
- Abstract
- Description
- Claims
- Application Information
AI Technical Summary
Problems solved by technology
Method used
Image
Examples
Embodiment 1
[0043] A display assembly, comprising a display screen 1, a first polyimide film 2 and a second polyimide film 3, wherein the first polyimide film 2 is pasted on the surface of the display screen 1 through an adhesive layer , the second polyimide film 3 is pasted on the surface of the first polyimide film 2 and deposited by electrodeposition. The first polyimide film 2 comprises the following raw material components in parts by weight: 80 parts of polyimide resin micropowder, 1 part of EDTA chelated manganese, 3 parts of silicon nitride micropowder, 10 parts of curing agent and 7 parts of bentonite. Wherein the curing agent is selected as dioctyl phthalate. Wherein the polyimide resin powder is selected as poly(pyromellitic dianhydride / 4,4 oxydiphenylamine / nonylphenol ethoxylate phosphate) copolymer.
[0044] The preparation method of the display screen assembly in this embodiment is as follows:
[0045] (1) Preparation of the first polyimide film: Weigh the raw materials in...
Embodiment 2
[0050] A display assembly, comprising a display screen 1, a first polyimide film 2 and a second polyimide film 3, wherein the first polyimide film 2 is pasted on the surface of the display screen 1 through an adhesive layer , the second polyimide film 3 is pasted on the surface of the first polyimide film 2 and deposited by electrodeposition. The first polyimide film 2 includes the following raw material components in parts by weight: 130 parts of polyimide resin micropowder, 3 parts of manganese chelated with EDTA, 6 parts of silicon nitride micropowder, 15 parts of curing agent and 15 parts of bentonite. The curing agent is a combination of 2,4-diamino-3,5-diethyl-toluene and 2,6-diamino-3,5-diethyl-toluene. Wherein the polyimide resin powder is selected as poly(biphenyltetracarboxylic dianhydride / 4,4'oxydiphenylamine / nonylphenol ethoxylate phosphate) copolymer.
[0051] The preparation method of the display screen assembly in this embodiment is as follows:
[0052] (1) Pr...
Embodiment 3
[0057] A display assembly, comprising a display screen 1, a first polyimide film 2 and a second polyimide film 3, wherein the first polyimide film 2 is pasted on the surface of the display screen 1 through an adhesive layer , the second polyimide film 3 is pasted on the surface of the first polyimide film 2 and deposited by electrodeposition. The first polyimide film 2 includes the following raw material components in parts by weight: 120 parts of polyimide resin micropowder, 2.5 parts of EDTA chelated manganese, 5 parts of silicon nitride micropowder, 14 parts of curing agent and 12 parts of bentonite. Among them, the curing agent is selected as methyl etherified amino resin. Wherein the polyimide resin powder is selected as poly(pyromellitic dianhydride / phenylenediamine / nonylphenol ethoxylate phosphate) copolymer.
[0058] The preparation method of the display screen assembly in this embodiment is as follows:
[0059] (1) Preparation of the first polyimide film: Weigh the ...
PUM
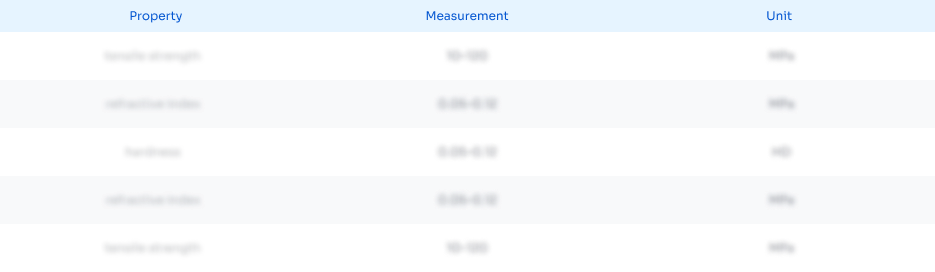
Abstract
Description
Claims
Application Information

- R&D Engineer
- R&D Manager
- IP Professional
- Industry Leading Data Capabilities
- Powerful AI technology
- Patent DNA Extraction
Browse by: Latest US Patents, China's latest patents, Technical Efficacy Thesaurus, Application Domain, Technology Topic, Popular Technical Reports.
© 2024 PatSnap. All rights reserved.Legal|Privacy policy|Modern Slavery Act Transparency Statement|Sitemap|About US| Contact US: help@patsnap.com