Catalyst for producing cyclopentene from cyclopentadiene, preparation method and application thereof
A technology for preparing cyclopentene and cyclopentadiene from cyclopentadiene is applied in the field of catalyst for preparing cyclopentene from cyclopentadiene and the field of preparation thereof, and can solve the problems of insufficient selectivity and low-temperature reaction activity, high mechanical strength ratio Surface area, easy spontaneous combustion and other problems, to achieve excellent selective hydrogenation effect of cyclopentadiene, high selectivity and low temperature activity, and mild reaction conditions
- Summary
- Abstract
- Description
- Claims
- Application Information
AI Technical Summary
Problems solved by technology
Method used
Image
Examples
Embodiment 1
[0042] A. TiO 2 -Al 2 o 3 Preparation of composite oxide supports
[0043] Take the BET specific surface area as 90m 2 / g, clover-shaped Al with a pore volume of 0.58ml / g and a most probable pore diameter of 13nm 2 o 3 100g, with 58mlTiO 2 Immerse in titanium sulfate solution with a content of 19.05g, let it stand for 10-30 minutes, dry at 110°C for 6 hours, and then bake at 500°C for 4 hours to obtain TiO 2 16 wt% TiO 2 -Al 2 o 3 Composite oxide carrier;
[0044] B. Preparation of catalyst
[0045] 100 g of the composite oxide carrier prepared above is dropped into 60 ml of nickel nitrate solution with NiO content of 11.5 g, immersed for 120-180 minutes, dried at 110° C. for 6 hours, and then calcined at 500° C. for 4 hours to obtain a NiO content of 10.3wt% catalyst precursor; 100g of the catalyst precursor was dropped into 65ml Ag content of 3.1g silver nitrate aqueous solution, immersed for 1 hour, dried at 110°C for 6 hours, and then calcined at 500°C for 4 hou...
Embodiment 2-4
[0047] The catalyst preparation method is the same as in Example 1, except that the content of NiO, the type and content of co-active components are changed to prepare catalysts C-2, C-3, C-4, C-5 and C-6 respectively.
Embodiment 5
[0049] Step A is the same as in Example 1.
[0050] Step B
[0051] 100 g of the composite oxide carrier prepared above was put into 65 ml of silver nitrate aqueous solution with an Ag content of 3.45 g, immersed for 1 hour, dried at 110°C for 6 hours, and then calcined at 500°C for 4 hours. Then 100 g of the roasted product was dropped into 60 ml of nickel nitrate solution with a NiO content of 11.1 g, immersed for 120-180 minutes, dried at 110° C. for 6 hours, and then calcined at 500° C. for 4 hours to obtain catalyst C-7.
PUM
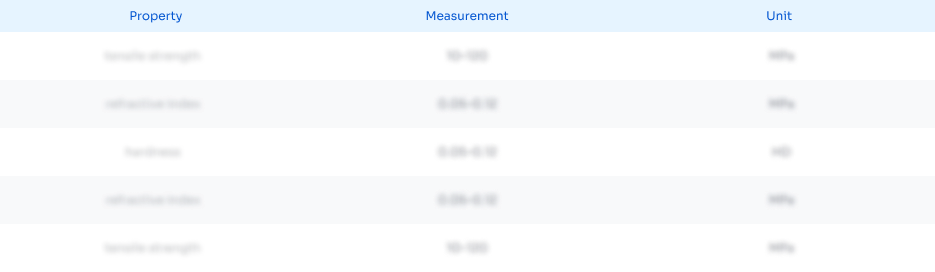
Abstract
Description
Claims
Application Information

- R&D Engineer
- R&D Manager
- IP Professional
- Industry Leading Data Capabilities
- Powerful AI technology
- Patent DNA Extraction
Browse by: Latest US Patents, China's latest patents, Technical Efficacy Thesaurus, Application Domain, Technology Topic, Popular Technical Reports.
© 2024 PatSnap. All rights reserved.Legal|Privacy policy|Modern Slavery Act Transparency Statement|Sitemap|About US| Contact US: help@patsnap.com