A sintering flue gas desulfurization and denitrification purification system and process
A desulfurization, denitrification, and purification system technology, applied in the field of flue gas purification, can solve problems such as low economic benefits, high energy consumption, and substandard emissions
- Summary
- Abstract
- Description
- Claims
- Application Information
AI Technical Summary
Problems solved by technology
Method used
Image
Examples
Embodiment 1
[0098] In the process of sintering flue gas desulfurization and denitration purification system, ozone is first introduced into the flue gas, and the nitric oxide in the flue gas reacts with ozone to oxidize nitric oxide into high-value nitrogen oxides; then the flue gas is sprayed Pre-wash, and then reduce the flue gas temperature to 60 °C; after pre-washing, the flue gas and ammonia water are subjected to absorption reaction to remove sulfur dioxide in the flue gas to obtain an intermediate product ammonium sulfite solution; After whitening, it is discharged to the atmosphere; the intermediate product ammonium sulfite solution is oxidized with compressed air, and the ammonium sulfite aqueous solution is oxidized into an ammonium sulfate solution; the ammonium sulfate solution is heated and concentrated to a saturated ammonium sulfate slurry with a solid content of 15%; Then, the saturated ammonium sulfate slurry is subjected to evaporative crystallization treatment, cyclone t...
Embodiment 2
[0100] In the process of sintering flue gas desulfurization and denitration purification system, ozone is first introduced into the flue gas, and the nitric oxide in the flue gas reacts with ozone to oxidize nitric oxide into high-value nitrogen oxides; then the flue gas is sprayed Pre-wash, and then reduce the flue gas temperature to 70 °C; after pre-washing, the flue gas is absorbed and reacted with ammonia water to remove the sulfur dioxide in the flue gas to obtain an intermediate product ammonium sulfite solution; After whitening, it is discharged to the atmosphere; the intermediate product ammonium sulfite solution is oxidized with compressed air, and the ammonium sulfite aqueous solution is oxidized into an ammonium sulfate solution; the ammonium sulfate solution is heated and concentrated to a saturated ammonium sulfate slurry with a solid content of 20%; Then, the saturated ammonium sulfate slurry is subjected to evaporative crystallization treatment, cyclone treatment...
Embodiment 3
[0102] In the process of sintering flue gas desulfurization and denitration purification system, ozone is first introduced into the flue gas, and the nitric oxide in the flue gas reacts with ozone to oxidize nitric oxide into high-value nitrogen oxides; then the flue gas is sprayed Pre-wash, and then reduce the flue gas temperature to 65 °C; after pre-washing, the flue gas is absorbed and reacted with ammonia water to remove the sulfur dioxide in the flue gas to obtain an intermediate product ammonium sulfite solution; After whitening, it is discharged to the atmosphere; the intermediate product ammonium sulfite solution is oxidized with compressed air, and the ammonium sulfite aqueous solution is oxidized into an ammonium sulfate solution; the ammonium sulfate solution is heated and concentrated to a saturated ammonium sulfate slurry with a solid content of 17%; Then, the saturated ammonium sulfate slurry is subjected to evaporative crystallization treatment, cyclone treatment...
PUM
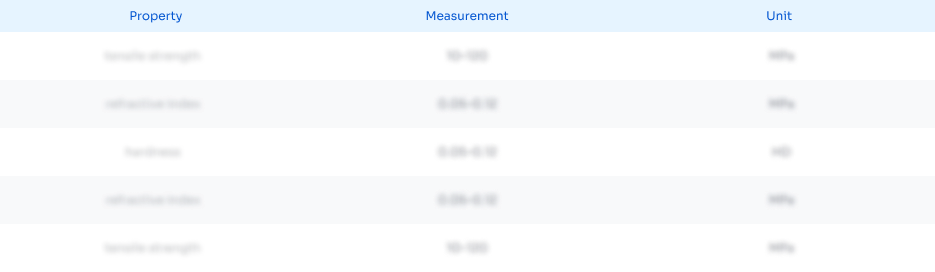
Abstract
Description
Claims
Application Information

- Generate Ideas
- Intellectual Property
- Life Sciences
- Materials
- Tech Scout
- Unparalleled Data Quality
- Higher Quality Content
- 60% Fewer Hallucinations
Browse by: Latest US Patents, China's latest patents, Technical Efficacy Thesaurus, Application Domain, Technology Topic, Popular Technical Reports.
© 2025 PatSnap. All rights reserved.Legal|Privacy policy|Modern Slavery Act Transparency Statement|Sitemap|About US| Contact US: help@patsnap.com