An automatic calibration method for permanent magnet synchronous motor
A permanent magnet synchronous motor, automatic calibration technology, applied in the direction of control generator, motor generator control, control electromechanical brake, etc., can solve the difficulty of simultaneously taking into account the maximum torque current maximum torque voltage ratio calibration, the voltage is not enough to adjust the current Size, system out of control and other problems, to achieve the effect of reducing equipment dependence and calibration costs, avoiding delays, and simplifying the process of torque acquisition
- Summary
- Abstract
- Description
- Claims
- Application Information
AI Technical Summary
Problems solved by technology
Method used
Image
Examples
Embodiment Construction
[0044] The technical solutions of the present invention will be described in further detail below with reference to the accompanying drawings and embodiments.
[0045] Such as Figure 1-2 As shown, the method includes the following steps:
[0046] Step 1. The dynamometer drives the calibrated permanent magnet synchronous motor to run at the set speed, calibrate the maximum torque current point of the permanent magnet synchronous motor at different speeds, and the calibrated permanent magnet synchronous motor at different speeds The optimal working point of the permanent magnet synchronous motor is not the same. It is necessary to select multiple speed points from zero speed to the maximum speed of the permanent magnet synchronous motor, record the optimal working point of the permanent magnet synchronous speed respectively, and set the initial value of the dynamometer, that is, set the first start the calibration process of the permanent magnet synchronous motor;
[0047] St...
PUM
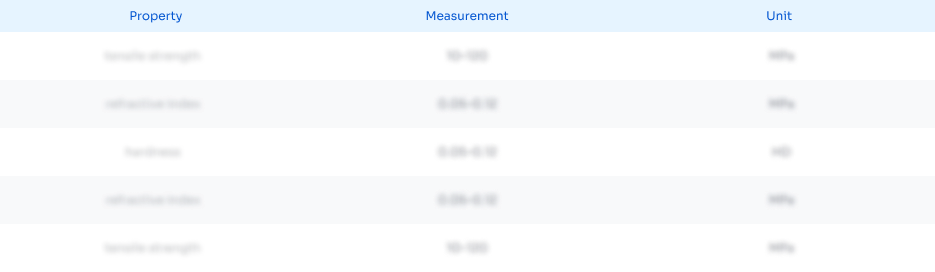
Abstract
Description
Claims
Application Information

- R&D
- Intellectual Property
- Life Sciences
- Materials
- Tech Scout
- Unparalleled Data Quality
- Higher Quality Content
- 60% Fewer Hallucinations
Browse by: Latest US Patents, China's latest patents, Technical Efficacy Thesaurus, Application Domain, Technology Topic, Popular Technical Reports.
© 2025 PatSnap. All rights reserved.Legal|Privacy policy|Modern Slavery Act Transparency Statement|Sitemap|About US| Contact US: help@patsnap.com