A full-order sliding mode observation device and method for permanent magnet synchronous motor rotor position
A technology of permanent magnet synchronous motor and full-order sliding mode, which is applied in the control of electromechanical transmission, control of generator, motor generator control, etc. It can solve the problems of accelerating error variables, reducing the chattering suppression effect of the control system, and occupying DSP. , to avoid the phase error problem, increase the accuracy of sliding mode observation, and highlight the effect of substantive characteristics
- Summary
- Abstract
- Description
- Claims
- Application Information
AI Technical Summary
Problems solved by technology
Method used
Image
Examples
Embodiment 1
[0043] Such as figure 1 with figure 2 As shown, a permanent magnet synchronous motor rotor position full-order sliding mode observation device, the device includes a full-order sliding mode observer 1, a saturation function processing module 2 and a phase-locked loop module 3;
[0044] The full-order sliding mode observer 1 is provided with the stator voltage u in two-phase static coordinates s Input terminal, rotor speed observation value Observation error of back EMF in input terminal and two-phase stationary coordinate system input terminal;
[0045] The stator current observation value of the full-order sliding mode observer 1 Output terminal and stator current value i s After making a difference, the sliding mode function control vector F (S) under the permanent magnet synchronous motor two-phase stationary coordinate system is output through the saturation function processing module 2; the sliding mode function control vector F (S) is passed through the sliding ...
Embodiment 2
[0075] Combine below figure 2 Describe the present embodiment. This embodiment is a further description of the full-order sliding mode observation method for the rotor position of the permanent magnet synchronous motor described in the first embodiment. In step 3, the sliding mode function control vector F(S) is passed through the sliding mode gain matrix G 1 The rear boundary layer changes in the form of figure 2 As shown, the observation error of the back electromotive force in the two-phase stationary coordinate system The expression is
[0076]
Embodiment 3
[0078] Combine below image 3 Describe this embodiment. This embodiment is a further description of the full-order sliding mode observation method for the rotor position of a permanent magnet synchronous motor described in Embodiment 1. The working principle of the phase-locked loop module in step 5 is as follows image 3 As shown, its working process is:
[0079] Step 51, Observing the rotor position of the permanent magnet synchronous motor After the cosine operation and the observed value of the α-axis back electromotive force multiplied, ie Observation of rotor position of permanent magnet synchronous motor After the sine operation and the observed value of the β-axis back electromotive force multiplied, ie
[0080] Step 52, for the obtained in step 51 with Perform heterodyne calculation to get the rotor position error signal κ of the permanent magnet synchronous motor after heterodyne processing
[0081]
[0082] Step 53: After the rotor position error ...
PUM
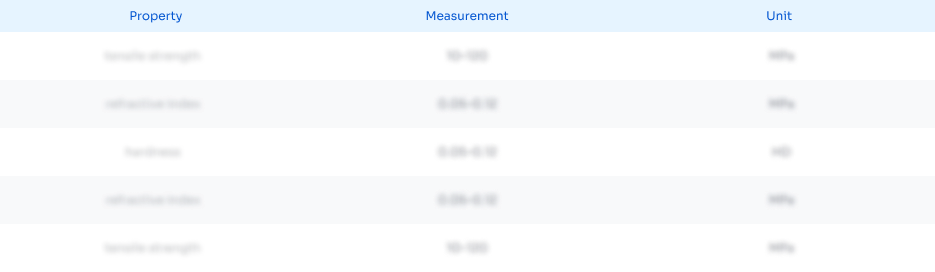
Abstract
Description
Claims
Application Information

- R&D
- Intellectual Property
- Life Sciences
- Materials
- Tech Scout
- Unparalleled Data Quality
- Higher Quality Content
- 60% Fewer Hallucinations
Browse by: Latest US Patents, China's latest patents, Technical Efficacy Thesaurus, Application Domain, Technology Topic, Popular Technical Reports.
© 2025 PatSnap. All rights reserved.Legal|Privacy policy|Modern Slavery Act Transparency Statement|Sitemap|About US| Contact US: help@patsnap.com