Machining technology method for miniature integrated impeller
A technology of integral impeller and machining process, applied in the direction of program control, instrumentation, electrical and digital data processing, etc., can solve the problems of difficult-to-machine structure, no proposed machining process, and no milling parameter selection and optimization part, so as to achieve optimal cutting parameters, the effect of improving processing stability
- Summary
- Abstract
- Description
- Claims
- Application Information
AI Technical Summary
Problems solved by technology
Method used
Image
Examples
Embodiment Construction
[0028] Such as figure 1 As shown, this embodiment relates to a processing method of a miniature integral impeller, and the specific steps include:
[0029] Step 1: Use CAM software to design and calculate the tool path and simulate the virtual machining process to prevent collisions and overcutting caused by unreasonable and wrong tool path planning from causing serious damage to the process system, and then determine through experiments Suitable tool inclination.
[0030] The virtual machining process simulation can effectively reduce the manufacturing cost of the product, shorten the product manufacturing cycle, and establish a simulation environment for the machining process system, which is extremely important for the numerical control machining of complex structures such as integral impellers.
[0031] During the machining process, with the change of the tool inclination angle, the tool and the workpiece surface will form different contact areas. Too small an inclination angle...
PUM
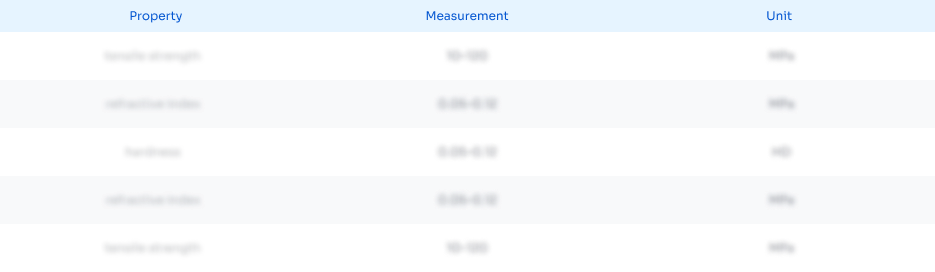
Abstract
Description
Claims
Application Information

- R&D Engineer
- R&D Manager
- IP Professional
- Industry Leading Data Capabilities
- Powerful AI technology
- Patent DNA Extraction
Browse by: Latest US Patents, China's latest patents, Technical Efficacy Thesaurus, Application Domain, Technology Topic, Popular Technical Reports.
© 2024 PatSnap. All rights reserved.Legal|Privacy policy|Modern Slavery Act Transparency Statement|Sitemap|About US| Contact US: help@patsnap.com