Inertial friction welding method based on preheating by friction
A technology of friction welding and process, applied in welding equipment, manufacturing tools, non-electric welding equipment, etc., can solve the problems of inability to form metallurgical bonding, inability to fully meet the thermal physical properties of high-strength alloy materials, welding of dissimilar metal materials, and low joint strength. It is beneficial to material flow and deformation, easy to fully automatic control, and optimizes the performance of joints
- Summary
- Abstract
- Description
- Claims
- Application Information
AI Technical Summary
Problems solved by technology
Method used
Image
Examples
Embodiment 1
[0039] Such as figure 1 , 2 , 3, using friction preheating inertial friction welding process to realize the connection of nickel-iron-based superalloy rods with a diameter of 10.5mm, including the following steps:
[0040] (1) HSMZ-4 axial friction welding machine is adopted, and the moment of inertia of the flywheel is 1.0kg m 2 , before starting welding, determine the pretightening force of 300MPa, the spindle speed of 1200rpm, the friction pressure of 300MPa, the friction shortening of 1mm, the upsetting pressure of 300MPa, and the holding time of 5s, and input the welding process parameters through the PC control interface 13;
[0041] (2) Welding starts: first, the hydraulic control system 12 adjusts the oil cylinder pressure to meet the parameter requirements, and the workpiece is clamped into the clamp of the friction welding machine, and a workpiece is clamped in each of the rotating end clamp 8 and the moving end clamp 7, and the workpiece, The rotating end and movi...
Embodiment 2
[0045] Such as figure 1 , 2 , 4, the inertial friction welding process of friction preheating is used to realize the connection of 37CrMoV alloy steel and 7075 aluminum alloy rods with a diameter of 10mm, including the following steps:
[0046] (1) HSMZ-4 axial friction welding machine is adopted, and the moment of inertia of the flywheel is 0.8kg m 2 , before the welding starts, determine the pretightening force of 20MPa, the spindle speed of 1600rpm, the friction pressure of 120MPa, the set value of the shortening amount of 1mm, the upsetting pressure of 120MPa, and the holding time of 15s, and input the welding control system 13 through the PC interface;
[0047] (2) Welding starts: first, the hydraulic control system 12 adjusts the oil cylinder pressure to meet the parameter requirements, and the workpiece is clamped into the clamp of the friction welding machine, and a workpiece is clamped in each of the rotating end clamp 8 and the moving end clamp 7, and the workpiece,...
PUM
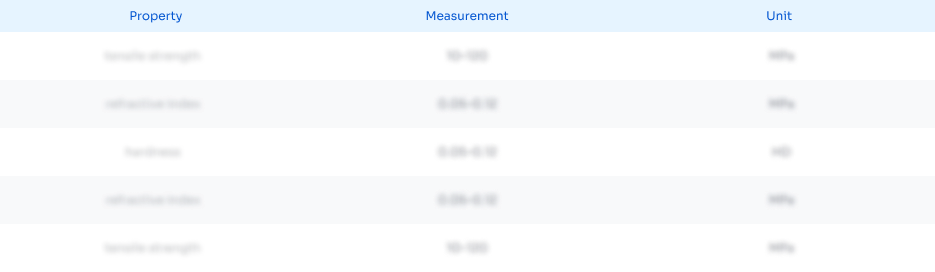
Abstract
Description
Claims
Application Information

- Generate Ideas
- Intellectual Property
- Life Sciences
- Materials
- Tech Scout
- Unparalleled Data Quality
- Higher Quality Content
- 60% Fewer Hallucinations
Browse by: Latest US Patents, China's latest patents, Technical Efficacy Thesaurus, Application Domain, Technology Topic, Popular Technical Reports.
© 2025 PatSnap. All rights reserved.Legal|Privacy policy|Modern Slavery Act Transparency Statement|Sitemap|About US| Contact US: help@patsnap.com