Process for extracting metal zinc from high-chlorine-content and high-zinc-content soot
A technology for extracting metals and processes, applied in the technical field of zinc recovery, can solve the problems of difficult to meet the electrolysis operation, unfavorable long-term development, high processing cost, and achieve the improvement of impurity removal rate and impurity removal rate, low cost, and improved particle size. Effect
- Summary
- Abstract
- Description
- Claims
- Application Information
AI Technical Summary
Problems solved by technology
Method used
Image
Examples
Embodiment 1
[0022] A process for extracting metal zinc from high chlorine-containing zinc soot, specifically:
[0023] Chlorine elution with zinc ash and alkali: the above-mentioned high chlorine-containing zinc soot recovery material is used in the countercurrent washing process of "one stage of alkali washing and one stage of water washing"; specifically, the washing liquid of the zinc ash alkali washing section is used as the pulping liquid for the zinc ash alkali washing, and the water washing The process uses new water as the pulping liquid; the washing time of alkali washing is 2 hours, the washing temperature is 85 °C, and the liquid-solid mass ratio is 3:1; the washing time of the water washing process is 1 hour, the washing temperature is 80 °C, and the liquid-solid mass ratio is 3 : 1; the washing liquid and the washing material are collected, the washing material is sent to leaching, and the washing liquid is evaporated and concentrated to obtain sodium chloride;
[0024] Leach...
Embodiment 2
[0031] A process for extracting metal zinc from high chlorine-containing zinc soot, specifically:
[0032] Chlorine elution with zinc ash and alkali: the above-mentioned high chlorine-containing zinc soot recovery material is used in the countercurrent washing process of "one stage of alkali washing and one stage of water washing"; specifically, the washing liquid of the zinc ash alkali washing section is used as the pulping liquid for the zinc ash alkali washing, and the water washing The process uses fresh water as the pulping liquid; the washing time of alkali washing is 2 hours, the washing temperature is 80 °C, and the liquid-solid mass ratio is 3:1; the washing time of the water washing process is 1 hour, the washing temperature is 80 °C, and the liquid-solid mass ratio is 3 : 1; the washing liquid and the washing material are collected, the washing material is sent to leaching, and the washing liquid is evaporated and concentrated to obtain sodium chloride;
[0033] Lea...
Embodiment 3
[0040] A process for extracting metal zinc from high chlorine-containing zinc soot, specifically:
[0041] Chlorine elution with zinc ash and alkali: the above-mentioned high chlorine-containing zinc soot recovery material is used in the countercurrent washing process of "one stage of alkali washing and one stage of water washing"; specifically, the washing liquid of the zinc ash alkali washing section is used as the pulping liquid for the zinc ash alkali washing, and the water washing The process uses new water as the pulping liquid; the washing time of alkali washing is 2 hours, the washing temperature is 90 ° C, and the liquid-solid mass ratio is 3:1; the washing time of the water washing process is 1 hour, the washing temperature is 80 ° C, and the liquid-solid mass ratio is 3 : 1; the washing liquid and the washing material are collected, the washing material is sent to leaching, and the washing liquid is evaporated and concentrated to obtain sodium chloride;
[0042] Lea...
PUM
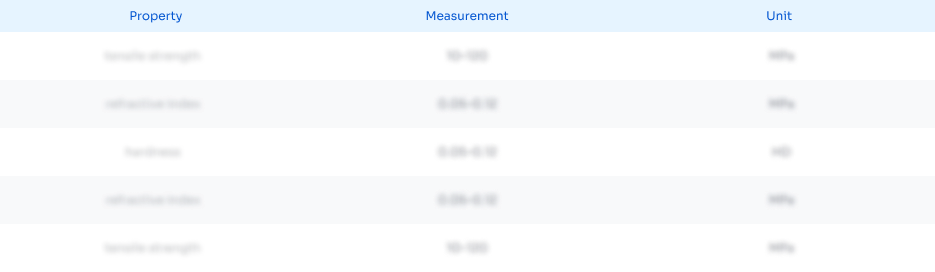
Abstract
Description
Claims
Application Information

- Generate Ideas
- Intellectual Property
- Life Sciences
- Materials
- Tech Scout
- Unparalleled Data Quality
- Higher Quality Content
- 60% Fewer Hallucinations
Browse by: Latest US Patents, China's latest patents, Technical Efficacy Thesaurus, Application Domain, Technology Topic, Popular Technical Reports.
© 2025 PatSnap. All rights reserved.Legal|Privacy policy|Modern Slavery Act Transparency Statement|Sitemap|About US| Contact US: help@patsnap.com