Manufacturing method of copper, cobalt nitride and carbon in-situ composite electrode
An in-situ composite, cobalt nitride technology, applied in battery electrodes, circuits, electrical components, etc., can solve problems such as upgrading and high price
- Summary
- Abstract
- Description
- Claims
- Application Information
AI Technical Summary
Problems solved by technology
Method used
Image
Examples
Embodiment 1
[0018] Electrodeposition was carried out in cobalt nitrate·hexahydrate and copper acetate·monowater solution at room temperature, in which the concentration of cobalt nitrate·hexahydrate was 75 mM, and the concentration of copper acetate·monohydrate was 75 mM, the voltage was -1.0 V, and the time was 180 s. After that, rinse repeatedly with deionized water and dry on a hot stage at 80°C for 10 min. Put the deposited carbon paper into a tube furnace, react at 400°C for 30 min under Air flow, and take it out after natural cooling to room temperature to form a porous, needle-shaped Cobalt oxide, copper oxide arrays. Tx-100 and dicyandiamide were dissolved in 2.0 mL N,N-dimethylformamide solution to obtain a precursor solution, wherein the amount of Tx-100 was 1.0 mL, and the concentration of dicyandiamide was 2000 mM. Soak the formed porous, needle-like cobalt oxide and copper oxide arrays in the precursor solution for 30 min, take it out, dry it on a hot table at 80°C for 10 mi...
Embodiment 2
[0021] Electrodeposition was carried out in cobalt nitrate hexahydrate and copper acetate monohydrate at room temperature, wherein the concentration of cobalt nitrate hexahydrate was 100 mM, and the concentration of copper acetate monohydrate was 50 mM, the voltage was -1.0 V, and the time was 180 s. After that, rinse repeatedly with deionized water and dry on a hot stage at 80°C for 10 min. Put the deposited carbon paper into a tube furnace, react at 400°C for 30 min under Air flow, and take it out after natural cooling to room temperature to form a porous, needle-shaped Cobalt oxide, copper oxide arrays. Dissolve Tx-100 and dicyandiamide in 2.0 mL of N,N-dimethylformamide solution to obtain a precursor solution, wherein the amount of Tx-100 is 1.0 mL, and the concentration of dicyandiamide is 2000 mM. Soak the formed porous, needle-like cobalt oxide and copper oxide arrays in the precursor solution for 30 minutes, take it out, dry it on a hot table at 80°C for 10 minutes, t...
Embodiment 3
[0028]Electrodeposition was carried out in cobalt nitrate hexahydrate and copper acetate monohydrate at room temperature, in which the concentration of cobalt nitrate hexahydrate was 112.5 mM, the concentration of copper acetate monohydrate was 37.5 mM, the voltage was -1.0 V, and the time was 180 s. Afterwards, rinse repeatedly with deionized water and dry at 80°C for 10 minutes on a hot table. Put the deposited carbon paper into a tube furnace, react at 400°C for 30 minutes under Air flow, and take it out after natural cooling to room temperature to form porous, needle-like oxidation Cobalt, copper oxide arrays. Tx-100 and dicyandiamide were dissolved in 2.0 mL N,N-dimethylformamide solution to obtain a precursor solution, wherein the amount of Tx-100 was 1.0 mL, and the concentration of dicyandiamide was 2000 mM. Soak the formed porous, needle-like cobalt oxide and copper oxide arrays in the precursor solution for 30 minutes, take it out, dry it on a hot table at 80°C for ...
PUM
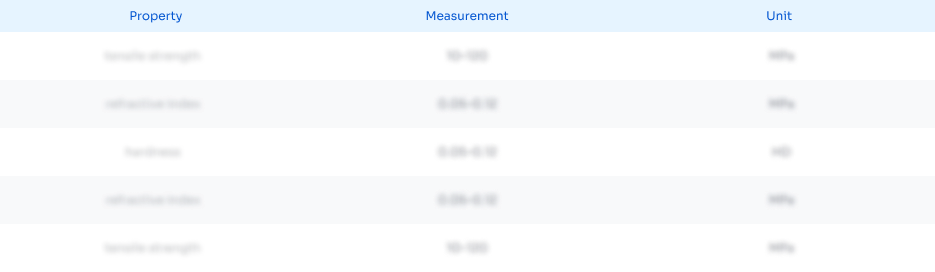
Abstract
Description
Claims
Application Information

- Generate Ideas
- Intellectual Property
- Life Sciences
- Materials
- Tech Scout
- Unparalleled Data Quality
- Higher Quality Content
- 60% Fewer Hallucinations
Browse by: Latest US Patents, China's latest patents, Technical Efficacy Thesaurus, Application Domain, Technology Topic, Popular Technical Reports.
© 2025 PatSnap. All rights reserved.Legal|Privacy policy|Modern Slavery Act Transparency Statement|Sitemap|About US| Contact US: help@patsnap.com