High corrosion resistance zinc-aluminum-magnesium hot-dip galvanized steel sheet and production method thereof
A production method and hot-dip plating technology, which are applied in hot-dip plating process, coating, metal material coating process and other directions, can solve the problems of insufficient welding performance and appearance of coating, high production cost, and high dipping temperature. Achieve the effect of increasing hardness, reducing surface oxidation and good surface quality
- Summary
- Abstract
- Description
- Claims
- Application Information
AI Technical Summary
Problems solved by technology
Method used
Image
Examples
Embodiment 1
[0022] Embodiment 1: The high-corrosion-resistant zinc-aluminum-magnesium hot-dip coated steel sheet and its production method are specifically described as follows.
[0023] Plating solution composition (wt): Al 1.8%, Mg 1.5%, RE 0.01%, Cu 0.003%, the rest is Zn and other uncontrollable impurities; Cu is added to the plating solution in the form of 60nm nano-copper when the plating solution melts .
[0024] Production process: the annealing temperature is 680°C; the dew point of the furnace nose is -10°C, the hot-dip plating temperature is 420°C, and the dipping time is 2 seconds; the cooling after plating is segmental cooling, and the temperature of the board surface is used as the control amount to adjust the opening of the fan; 10°C / S rapid cooling above 400°C, 3°C / S slow cooling from 400°C to 350°C, and 10°C / S rapid cooling below 350°C; the flattening elongation of the flattening process is 0.5%.
[0025] tested by figure 1 Visible, the organization of this method gaine...
Embodiment 2
[0026] Embodiment 2: The high-corrosion-resistant zinc-aluminum-magnesium hot-dipped steel sheet and its production method are specifically described as follows.
[0027] Plating solution composition (wt): Al 1.9%, Mg 1.2%, RE 0.03%, Cu 0.004%, the rest is Zn and other uncontrollable impurities; Cu is added to the plating solution in the form of 80nm nano-copper when the plating solution melts .
[0028] Production process: the annealing temperature is 690°C; the dew point of the furnace nose is -12°C; the hot-dip plating temperature is 430°C; Above 400°C is 14°C / S rapid cooling, 400°C~350°C is 3°C / S slow cooling, below 350°C is 12°C / S rapid cooling; flat elongation is 0.7%.
[0029] After testing, the structure of the coating obtained by this method is primary zinc, Zn / MgZn 2 Binary eutectic, Zn / Al / MgZn 2 Ternary eutectic and nano-copper; the coating hardness of the obtained steel plate and the red rust time in the salt spray test are shown in Table 1.
Embodiment 3
[0030] Embodiment 3: The high-corrosion-resistant zinc-aluminum-magnesium hot-dipped steel sheet and its production method are specifically described as follows.
[0031] Plating solution composition (wt): Al 2.0%, Mg 1.6%, RE 0.07%, Cu 0.008%, the rest is Zn and other uncontrollable impurities; Cu is added to the plating solution in the form of 20nm nano-copper when the plating solution melts .
[0032] Production process: the annealing temperature is 710°C; the dew point of the furnace nose is -18°C; the hot-dip plating temperature is 440°C; Above 400°C is 20°C / S rapid cooling, 400°C-350°C is 5°C / S slow cooling, below 350°C is 16°C / S rapid cooling; flat elongation is 0.9%.
[0033] After testing, the structure of the coating obtained by this method is primary zinc, Zn / MgZn 2 Binary eutectic, Zn / Al / MgZn 2 Ternary eutectic and nano-copper; the coating hardness of the obtained steel plate and the red rust time in the salt spray test are shown in Table 1.
PUM
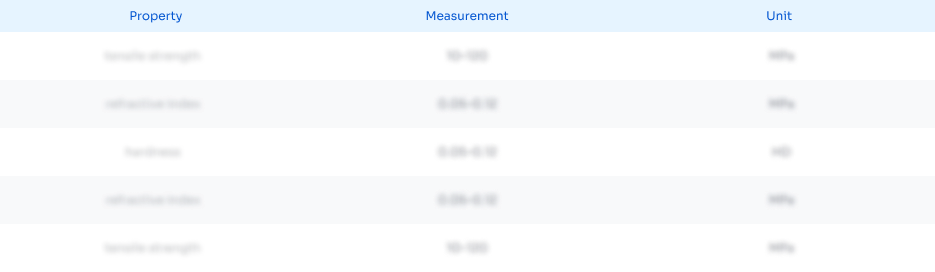
Abstract
Description
Claims
Application Information

- Generate Ideas
- Intellectual Property
- Life Sciences
- Materials
- Tech Scout
- Unparalleled Data Quality
- Higher Quality Content
- 60% Fewer Hallucinations
Browse by: Latest US Patents, China's latest patents, Technical Efficacy Thesaurus, Application Domain, Technology Topic, Popular Technical Reports.
© 2025 PatSnap. All rights reserved.Legal|Privacy policy|Modern Slavery Act Transparency Statement|Sitemap|About US| Contact US: help@patsnap.com