Recovery process for purifying sulfur with coal-to-methanol synthesis gas
A technology for gas purification of sulfur and coal to methanol, applied in the chemical industry, sustainable manufacturing/processing, inorganic chemistry, etc., to achieve the effects of avoiding temperature imbalance, facilitating production recovery, and facilitating operation and control
- Summary
- Abstract
- Description
- Claims
- Application Information
AI Technical Summary
Problems solved by technology
Method used
Image
Examples
Embodiment 1
[0075] A coal-to-methanol synthesis gas purification sulfur recovery process, including the temperature rise of the catalyst, the synthesis of elemental sulfur, and sulfur sweeping after the device is shut down, specifically including the following steps:
[0076] (1) The temperature rise of the catalyst:
[0077] Replace the sulfur recovery and nitrogen heating system, and the replacement will end when the gas analysis index reaches the combustible gas volume content ≤ 0.05% before the sulfur recovery catalyst starts to heat up; the qualified standard for the replacement is CO, H in the system 2 、H 2 S, CH 3 OH total volume content≤0.05%;
[0078] Use a nitrogen heater to raise the temperature of the catalyst bed of the sulfur recovery unit at a heating rate of 30-40°C / h. When the inlet temperature of the catalyst bed rises to 80±10°C, keep the temperature constant for 2 hours to remove physically adsorbed water and level the catalyst bed at the same time. Layer temperatur...
Embodiment 2
[0101] A coal-to-methanol synthesis gas purification sulfur recovery process, including the temperature rise of the catalyst, the synthesis of elemental sulfur, and sulfur sweeping after the device is shut down, including the following steps:
[0102] (1) The temperature rise of the catalyst:
[0103] Replace the sulfur recovery and nitrogen heating system, and the replacement ends when the gas analysis index reaches the combustible gas volume content ≤ 0.05% before the sulfur recovery catalyst starts to heat up;
[0104] Use a nitrogen heater to raise the temperature of the catalyst bed of the sulfur recovery unit at a heating rate of 30-40°C / h. When the inlet temperature of the catalyst bed rises to 80±10°C, keep the temperature constant for 2 hours to remove physically adsorbed water and level the catalyst bed at the same time. Layer temperature; control the inlet temperature of the catalyst bed to 120±10°C at a heating rate of 30-40°C / h, and keep the temperature constant f...
PUM
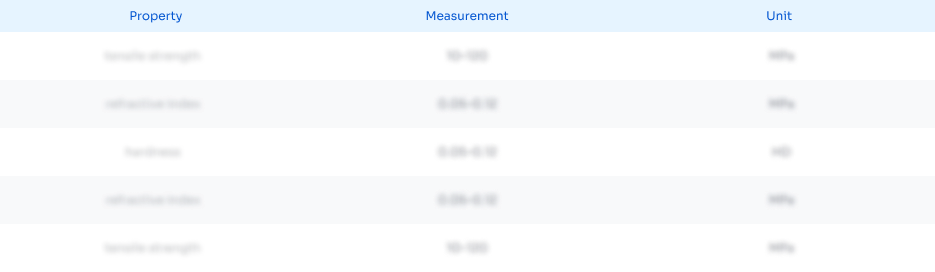
Abstract
Description
Claims
Application Information

- R&D Engineer
- R&D Manager
- IP Professional
- Industry Leading Data Capabilities
- Powerful AI technology
- Patent DNA Extraction
Browse by: Latest US Patents, China's latest patents, Technical Efficacy Thesaurus, Application Domain, Technology Topic, Popular Technical Reports.
© 2024 PatSnap. All rights reserved.Legal|Privacy policy|Modern Slavery Act Transparency Statement|Sitemap|About US| Contact US: help@patsnap.com