A coating welding ring and its preparation method
A coating and welding ring technology, used in welding equipment, manufacturing tools, welding media, etc., can solve the problems of poor surface coating adhesion, insufficient surface brazing amount, and surface coating loss, etc., to achieve adhesion and thickness. Good stability, strong skin adhesion, easy to assemble and use
- Summary
- Abstract
- Description
- Claims
- Application Information
AI Technical Summary
Problems solved by technology
Method used
Image
Examples
Embodiment 1
[0030] 1) Mix polyurethane, butyl acetate 3, acetone 3, and dimethyl carbonate at a mass ratio of 85%: 3%: 3%: 9%, heat to 80°C and stir to form a binder;
[0031] 2) Soak the solder ring in the binder and take it out after soaking for 5 minutes;
[0032] 3) Pour the brazing material ring and FB105 brazing flux into a low-speed centrifuge, the quality of the brazing flux is one-tenth of the brazing filler metal, and the centrifuge runs at a speed of 500 rpm for 3 minutes;
[0033] 4) Put the semi-finished product (the semi-finished product of the coating welding ring, the same below) into the three-dimensional vibration grinder, add zirconia ball milling beads, the mass of the ball milling beads is half of the mass of the solder, blow in hot air, and after 5 minutes take out.
Embodiment 2
[0035] 1) Synthesize polyurethane and acetone into a binder at a mass ratio of 90%:10% and stir evenly;
[0036] 2) Put the solder ring in the vibrating machine, spray the prepared binder while starting the vibrating machine, and take it out after 5 minutes;
[0037] 3) Pour the solder ring and FB105 flux into a low-speed centrifuge, the mass of the flux is one-tenth of the mass of the solder, and the centrifuge runs at a speed of 500 rpm for 3 minutes;
[0038] 4) Put the semi-finished product into the three-dimensional vibration grinder, add zirconia ball milling beads, the mass of the ball milling beads is half of the mass of the solder ring, blow in hot air, and take it out after 5 minutes.
Embodiment 3
[0040] 1) Polyurethane and dimethyl carbonate are synthesized into a binder at a mass ratio of 85%:15%;
[0041] 2) Soak the solder ring in the binder and take it out after soaking for 5 minutes;
[0042] 3) Pour the solder ring and FB105 flux into a low-speed centrifuge, the mass of the flux is one-fifth of the mass of the solder, and the centrifuge runs at a speed of 500 rpm for 3 minutes;
[0043] 4) Put the semi-finished product into the three-dimensional vibration grinder, add zirconia ball milling beads, the quality of the ball milling beads is equal to that of the solder, blow in hot air, and take it out after 5 minutes.
[0044]
PUM
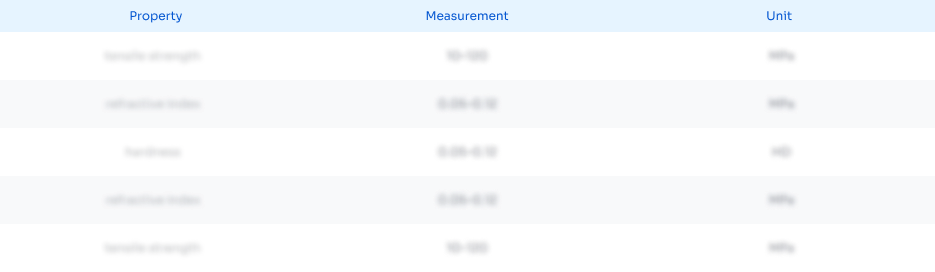
Abstract
Description
Claims
Application Information

- Generate Ideas
- Intellectual Property
- Life Sciences
- Materials
- Tech Scout
- Unparalleled Data Quality
- Higher Quality Content
- 60% Fewer Hallucinations
Browse by: Latest US Patents, China's latest patents, Technical Efficacy Thesaurus, Application Domain, Technology Topic, Popular Technical Reports.
© 2025 PatSnap. All rights reserved.Legal|Privacy policy|Modern Slavery Act Transparency Statement|Sitemap|About US| Contact US: help@patsnap.com