Preparation method for carbon-coated modified high-multiplying-power titanium-niobium oxide material
A titanium-niobium oxide, high-rate technology, applied in electrochemical generators, electrical components, battery electrodes, etc., can solve the problems of low ionic conductivity and electrochemical performance, improve electrochemical performance and reduce primary particle size , The effect of increasing the specific surface area
- Summary
- Abstract
- Description
- Claims
- Application Information
AI Technical Summary
Problems solved by technology
Method used
Image
Examples
Embodiment 1
[0023] The preparation method of the carbon-coated modified high-magnification titanium-niobium oxide material in this embodiment is as follows:
[0024] Add 7.5 g of titanium dioxide, 26.5 g of niobium pentoxide, and 0.5 g of glucose into 100 g of deionized water one by one, and stir evenly to obtain a mixed solution A.
[0025] Mixture A was ball milled at 600 r / min for 48 h, and then spray-dried and granulated at an inlet temperature of 260 °C and an outlet temperature of 60 °C. The spray-dried material was pre-sintered at 500 °C for 6 h in a nitrogen atmosphere, and then calcined at 800 °C for 20 h to obtain a carbon-coated modified high-magnification titanium-niobium oxide material C@TiNb 2 o 7 .
[0026] Using the scheme of Example 1, three experiments were conducted in parallel, and the obtained products were numbered A, B, and C respectively, and CR2032-type simulated batteries were produced, and the capacity was tested. The test results are shown in Table 1.
[002...
Embodiment 2
[0031] The preparation method of the carbon-coated modified high-magnification titanium-niobium oxide material in this embodiment is as follows:
[0032]Add 34.0 g of tetra-n-butyl titanate, 135.1 g of niobium pentachloride, and 1.2 g of polyethylene glycol into 200 g of deionized water one by one, and stir evenly to obtain a mixed solution A.
[0033] Mixture A was ball milled at 1200 r / min for 24 h, and then spray-dried and granulated at an inlet temperature of 300 °C and an outlet temperature of 100 °C. The spray-dried material was pre-sintered at 550 °C for 2 h in a nitrogen atmosphere, and then calcined at 1300 °C for 8 h to obtain a carbon-coated modified high-magnification titanium-niobium oxide material C@Ti 2 Nb 10 o 29 .
Embodiment 3
[0035] The preparation method of the carbon-coated modified high-magnification titanium-niobium oxide material in this embodiment is as follows:
[0036] 28.4 g of tetraisopropyl titanate, 107.6 g of niobium oxalate hydrate, and 2.0 g of polyvinylpyrrolidone were successively added to 200 g of deionized water and stirred evenly to obtain a mixed solution A.
[0037] Mixture A was ball milled at 800 r / min for 36 h, and then spray-dried and granulated at an inlet temperature of 280 °C and an outlet temperature of 80 °C. The spray-dried material was pre-sintered at 520 °C for 3 h in a nitrogen atmosphere, and then calcined at 900 °C for 15 h to obtain a carbon-coated modified high-magnification titanium-niobium oxide material C@TiNb 2 o 7 .
PUM
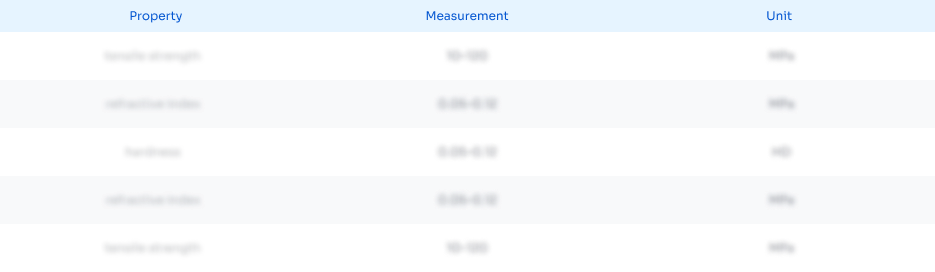
Abstract
Description
Claims
Application Information

- R&D Engineer
- R&D Manager
- IP Professional
- Industry Leading Data Capabilities
- Powerful AI technology
- Patent DNA Extraction
Browse by: Latest US Patents, China's latest patents, Technical Efficacy Thesaurus, Application Domain, Technology Topic, Popular Technical Reports.
© 2024 PatSnap. All rights reserved.Legal|Privacy policy|Modern Slavery Act Transparency Statement|Sitemap|About US| Contact US: help@patsnap.com