Dissolvable printing ink, method for protecting surface of used material through dissolvable printing ink during brazing process and application of dissolvable printing ink
An ink and vinyl resin technology, applied in the field of dissolvable ink, can solve the problems of complicated and complicated preparation process, difficult to commercialize, consuming manpower and financial resources, etc., and achieves the effects of convenient construction, prevention of stains or spots, and low price.
- Summary
- Abstract
- Description
- Claims
- Application Information
AI Technical Summary
Problems solved by technology
Method used
Image
Examples
Embodiment 1
[0038] Take 12.42g gamma-butyrolactone, 4.2g polyethylene acetate resin, 2.1g trioctyl trimellitate, 1.2g polytetrafluoroethylene wax, 1.0g quartz powder, 0.0164g phthalocyanine blue, mix them at high speed Disperse and stir for 20 minutes with a disperser, then completely homogenize through a three-roller mill, screen-print on the object to be used, and place it in a blast drying oven at 150°C for about 10 minutes to completely solidify to form a coating.
[0039] The coating exhibits good resistance to nickel / gold plating. The coating in this experimental example is put into a pre-configured heated chemical nickel plating solution (85°C), soaked in the chemical gold plating solution (90°C) 30min, 10min washing and air-drying, no swelling, peeling and discoloration of the film layer occurred through visual inspection, and there was no nickel / gold penetration on the surface of the circuit board after the film was removed.
[0040] The coating can withstand 5 minutes at 170°C, ...
Embodiment 2
[0043] Take 11.42g gamma-butyrolactone, 4.2g polyvinyl chloride resin, 2.2g trioctyl trimellitate, 1.2g polytetrafluoroethylene wax, 1.0g quartz powder, 0.0164g phthalocyanine blue, mix them in a high-speed disperser Disperse and stir for 20 minutes, then pass through a three-roll mill to completely homogenize, screen-print on the object to be used, and place it in a blast drying oven at 150°C for about 5 minutes to completely solidify to form a coating.
[0044] The coating exhibits good resistance to nickel / gold plating. The coating in this experimental example is put into a pre-configured heated chemical nickel plating solution (85°C), soaked in the chemical gold plating solution (90°C) 30min, 10min washing and air-drying, no swelling, peeling and discoloration of the film layer occurred through visual inspection, and there was no nickel / gold penetration on the surface of the circuit board after the film was removed.
[0045] The coating can withstand 5 minutes at 170°C, no...
Embodiment 3
[0048] Take 13.42g γ-butyrolactone, 4.5g polyvinyl acetate, 2.0g dimethyl phthalate, 1.1g polytetrafluoroethylene wax, 1.1g quartz powder, 0.0164g phthalocyanine blue, mix and disperse at high speed Machine dispersion and stirring for 20 minutes, and then completely homogenized by a three-roller mill, screen printed on the object to be used, and placed in a blast drying oven at 150°C for about 5 minutes to completely solidify to form a coating.
[0049] The coating exhibits good resistance to nickel / gold plating. The coating in this experimental example is put into a pre-configured heated chemical nickel plating solution (85°C), soaked in the chemical gold plating solution (90°C) 30min, 10min washing and air-drying, no swelling, peeling and discoloration of the film layer occurred through visual inspection, and there was no nickel / gold penetration on the surface of the circuit board after the film was removed.
[0050] The coating can withstand 5 minutes at 170°C, and the film...
PUM
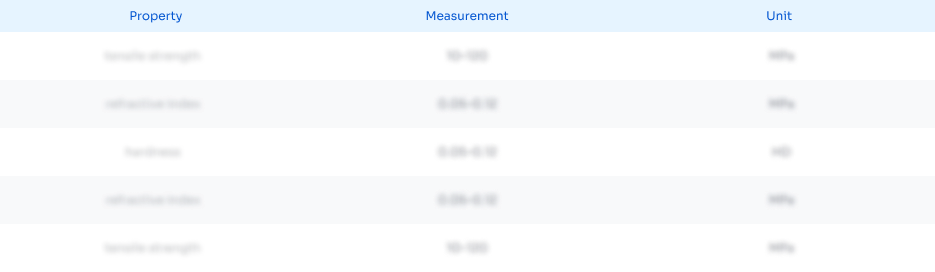
Abstract
Description
Claims
Application Information

- Generate Ideas
- Intellectual Property
- Life Sciences
- Materials
- Tech Scout
- Unparalleled Data Quality
- Higher Quality Content
- 60% Fewer Hallucinations
Browse by: Latest US Patents, China's latest patents, Technical Efficacy Thesaurus, Application Domain, Technology Topic, Popular Technical Reports.
© 2025 PatSnap. All rights reserved.Legal|Privacy policy|Modern Slavery Act Transparency Statement|Sitemap|About US| Contact US: help@patsnap.com