High casting speed continuous casting method of small billet directly rolled from long product
A small billet and direct technology, applied in the field of steelmaking and continuous casting, can solve the problems of high production cost and the surface temperature of the casting billet cannot meet the requirements of direct rolling, and achieve the effects of reducing the cooling strength, increasing the pulling speed, and increasing the surface temperature.
- Summary
- Abstract
- Description
- Claims
- Application Information
AI Technical Summary
Problems solved by technology
Method used
Image
Examples
Embodiment 1
[0023] A billet high-speed continuous casting method for direct rolling of long products. This embodiment takes the long steel production line of Shougang as an example to realize high-speed continuous casting of billets. The specific steps and parameters are as follows:
[0024] 1. The billet continuous casting machine is a 6-machine, 6-strand full-arc 150mm×150mm billet continuous casting machine, with a base arc radius R10.3m;
[0025] 2. [P]: 0.0130wt%, [S]: 0.0040wt% in steel;
[0026] 3. The casting speed of the continuous casting machine is controlled at 3.3m / min;
[0027] 4. The temperature of molten steel in the tundish is controlled at 1542°C;
[0028] 5. Crystallizer cooling water flow rate: 130m 3 / h;
[0029] 6. The secondary cooling adopts automatic water distribution, and the specific water volume is 1.15L / kg;
[0030] 7. Crystallizer electromagnetic stirring parameters: frequency 4.0Hz, current 250A;
[0031] 8. Ensure that the temperature of the head of t...
PUM
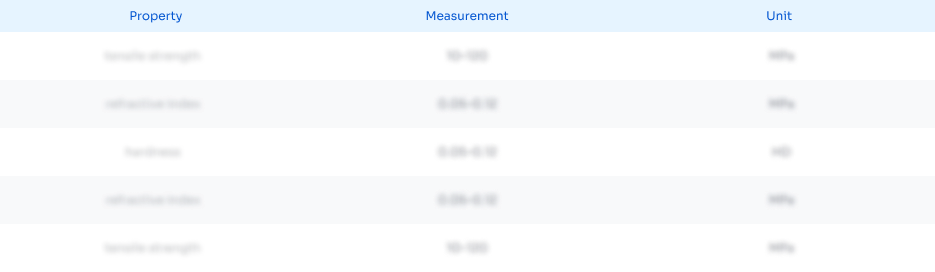
Abstract
Description
Claims
Application Information

- R&D Engineer
- R&D Manager
- IP Professional
- Industry Leading Data Capabilities
- Powerful AI technology
- Patent DNA Extraction
Browse by: Latest US Patents, China's latest patents, Technical Efficacy Thesaurus, Application Domain, Technology Topic, Popular Technical Reports.
© 2024 PatSnap. All rights reserved.Legal|Privacy policy|Modern Slavery Act Transparency Statement|Sitemap|About US| Contact US: help@patsnap.com