Continuous steel billet casting process and apparatus
A thin slab and continuous casting technology, which is applied to the continuous casting of thin slabs and the continuous casting device used for the same, can solve problems such as damage to the quality of thin slabs, impossibility of pouring molten steel, influence on drawing speed and output, etc. Leakage and shutdown accidents, realize the effect of molten steel protection pouring, and improve the pulling speed and output
- Summary
- Abstract
- Description
- Claims
- Application Information
AI Technical Summary
Problems solved by technology
Method used
Image
Examples
Embodiment Construction
[0020] The present invention provides a continuous casting method for thin slabs. It is provided with an inert gas protection zone between the tundish 2 and the crystallizer 3 of the continuous casting device, and the inert gas in the inert gas protection zone maintains a certain pressure. , can realize molten steel protection pouring. The inner hole of the upper orifice plate 17 of the crystallizer 3 remains unblocked. When the mold 3 is working, the inner cavity and the billet shell are kept lubricated, especially the large and small surfaces are evenly lubricated and must not stick. The nozzle center of the tundish 2 and the The center of the inner cavity of the crystallizer 3 should be on the same axis, and the shell thickness of the liquid core thin slab must be uniform.
[0021] According to Figure 1, Figure 2, image 3 , Figure 4 and Figure 5 , the present invention provides a continuous casting device for thin slabs, which includes a tundish 2, a crystallizer 3, a ...
PUM
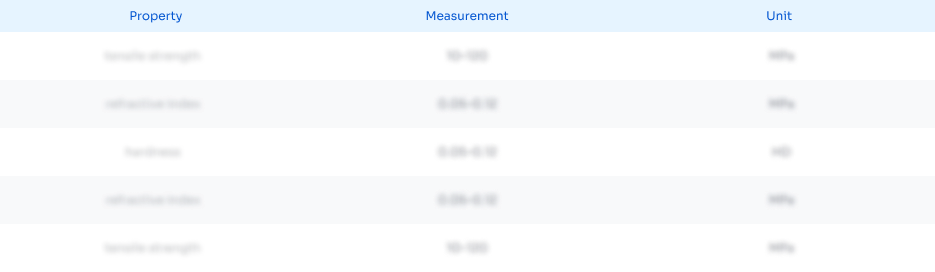
Abstract
Description
Claims
Application Information

- R&D Engineer
- R&D Manager
- IP Professional
- Industry Leading Data Capabilities
- Powerful AI technology
- Patent DNA Extraction
Browse by: Latest US Patents, China's latest patents, Technical Efficacy Thesaurus, Application Domain, Technology Topic, Popular Technical Reports.
© 2024 PatSnap. All rights reserved.Legal|Privacy policy|Modern Slavery Act Transparency Statement|Sitemap|About US| Contact US: help@patsnap.com