Anti-corrosion wear-resistant rubber material and preparation method thereof
A rubber material, anti-corrosion and wear-resistant technology, applied in the field of rubber materials, can solve the problems of limited anti-corrosion performance and wear resistance, and achieve the effects of good flex resistance and dynamic performance, good wear resistance and high elasticity
- Summary
- Abstract
- Description
- Claims
- Application Information
AI Technical Summary
Problems solved by technology
Method used
Examples
Embodiment 1
[0020] An anti-corrosion and wear-resistant rubber material, made of the following raw materials in parts by weight: 20 parts of neoprene rubber, 60 parts of butadiene rubber, 15 parts of ammonium polyphosphate, 50 parts of phenolic resin, 7 parts of white carbon black, 5 parts of silane di Joint agent, 8 parts of bamboo fiber, 2 parts of polypropylene fiber, 2 parts of magnesium oxide powder, 4 parts of zinc oxide powder, 3 parts of stearic acid, 6 parts of naphthenic oil, 1 part of anti-aging agent, 7 parts of accelerator, 2 parts Vulcanizing agent, 5 parts of diphenylsilanediol, 2 parts of resole phenolic resin.
[0021] A method for preparing an anti-corrosion and wear-resistant rubber material, comprising the following steps:
[0022] (1) Add bamboo fiber and polypropylene fiber into the container according to the mass ratio of 8:1, add ammonium polyphosphate powder and resole phenolic resin, mix evenly, heat press in a hot press at 140°C for 50 minutes, and set aside;
...
Embodiment 2
[0026] An anti-corrosion and wear-resistant rubber material, made of the following raw materials in parts by weight: 30 parts of neoprene rubber, 50 parts of butadiene rubber, 20 parts of ammonium polyphosphate, 35 parts of phenolic resin, 15 parts of white carbon black, 1 part of silane di Joint agent, 16 parts of bamboo fiber, 1 part of polypropylene fiber, 5 parts of magnesium oxide powder, 1 part of zinc oxide powder, 8 parts of stearic acid, 1 part of naphthenic oil, 4 parts of anti-aging agent, 2 parts of accelerator, 6 parts Vulcanizing agent, 1 part of diphenylsilanediol, 8 parts of resole phenolic resin.
[0027] A method for preparing an anti-corrosion and wear-resistant rubber material, comprising the following steps:
[0028] (1) Add bamboo fiber and polypropylene fiber into the container according to the mass ratio of 8:1, add ammonium polyphosphate powder and resole phenolic resin, mix evenly, heat press in a hot press at 145°C for 40 minutes, and set aside;
[...
Embodiment 3
[0032] An anti-corrosion and wear-resistant rubber material, made of the following raw materials in parts by weight: 22 parts of neoprene rubber, 55 parts of butadiene rubber, 17 parts of ammonium polyphosphate, 45 parts of phenolic resin, 10 parts of white carbon black, 4 parts of silane di Joint agent, 8 parts of bamboo fiber, 2 parts of polypropylene fiber, 3 parts of magnesium oxide powder, 3 parts of zinc oxide powder, 5 parts of stearic acid, 5 parts of naphthenic oil, 2 parts of anti-aging agent, 5 parts of accelerator, 4 parts Vulcanizing agent, 4 parts of diphenylsilanediol, 3 parts of resole phenolic resin.
[0033] A method for preparing an anti-corrosion and wear-resistant rubber material, comprising the following steps:
[0034] (1) Add bamboo fiber and polypropylene fiber into the container according to the mass ratio of 8:1, add ammonium polyphosphate powder and resole phenolic resin, mix evenly, heat press in a hot press at 140°C for 40 minutes, and set aside; ...
PUM
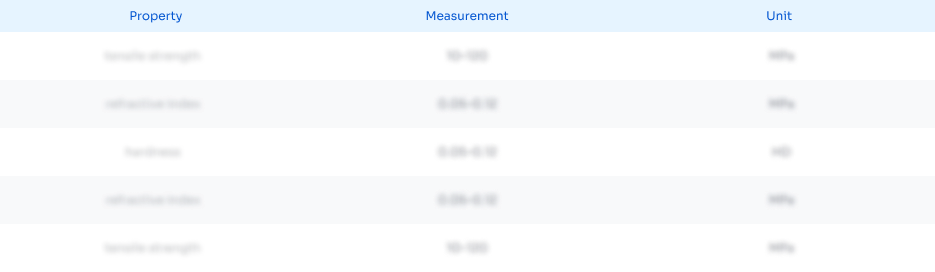
Abstract
Description
Claims
Application Information

- Generate Ideas
- Intellectual Property
- Life Sciences
- Materials
- Tech Scout
- Unparalleled Data Quality
- Higher Quality Content
- 60% Fewer Hallucinations
Browse by: Latest US Patents, China's latest patents, Technical Efficacy Thesaurus, Application Domain, Technology Topic, Popular Technical Reports.
© 2025 PatSnap. All rights reserved.Legal|Privacy policy|Modern Slavery Act Transparency Statement|Sitemap|About US| Contact US: help@patsnap.com