Hydrocracking method
A hydrocracking and hydrofining technology, which is applied in the fields of hydrotreating process, petroleum industry, hydrocarbon oil treatment products, etc., can solve the problems of complex operation of the unit, high yield of light hydrocarbons, complex operation, etc.
- Summary
- Abstract
- Description
- Claims
- Application Information
AI Technical Summary
Problems solved by technology
Method used
Image
Examples
Embodiment 1
[0042] (1) Take 200 g of the original NaY molecular sieve powder prepared in the laboratory, mix it with ammonium chloride with a concentration of 2.5 mol / L according to the liquid-solid ratio of 5:1, and exchange it at 85 °C for 2 hours. Repeat this process twice. The Na content in the molecular sieve is expressed as Na 2 O is calculated as 1.3%;
[0043] (2) Hydrothermal treatment of the Y molecular sieve obtained in step (1) at 530°C and 0.15Mpa for 1.5 hours;
[0044] (3) The Y molecular sieve obtained in step (2) was mixed with sodium nitrate with a concentration of 1.5 mol / L according to a liquid-solid ratio of 5:1, exchanged at 80 °C for 1 hour, and this process was repeated twice. The content is 3.6% as Na2O;
[0045] (4) The molecular sieve obtained in step (3) is mixed and beaten with ammonium fluorosilicate solution with a concentration of 0.5mol / L according to the liquid-solid ratio of 5:1, and treated at 95°C for 2 hours;
[0046] (5) The Y molecular sieve trea...
Embodiment 2
[0052] (1) Take 200 g of the original NaY molecular sieve powder prepared in the laboratory, mix with ammonium nitrate with a concentration of 1.6 mol / L according to the liquid-solid ratio of 3:1, exchange at 80 °C for 2 hours, repeat this process twice, the Y molecular sieve after exchange Na content in Na 2 O counts as 2.0%;
[0053] (2) Hydrothermal treatment of the Y molecular sieve obtained in step (1) at 550°C and 0.2MPa for 2 hours;
[0054] (3) The Y molecular sieve obtained in step (2) was mixed with a mixed solution containing sodium nitrate and glycerol at a ratio of 3.0 mol / L and 0.2 mol / L, respectively, according to a liquid-solid ratio of 5:1, exchanged at 80 °C for 1 hour, and repeated. This process is performed twice, and the Na content in the Y molecular sieve after exchange is equal to Na 2 O is calculated as 5.3%;
[0055] (4) The molecular sieve obtained in step (3) is mixed and beaten with an ammonium fluorosilicate solution with a concentration of 0.7 ...
Embodiment 3
[0062] With embodiment 1, just after obtaining Y-2, carry out following treatment: under stirring condition, Y molecular sieve and tetrapropyl ammonium hydroxide solution are mixed in autoclave, feed nitrogen to control system pressure at 0.4 MPa, then heat up to 70°C, continue stirring at constant temperature for 1 hour, release the pressure, cool, suction filter to pH less than 9, dry at 125°C for 12 hours, and calcinate at 500°C for 3 hours to obtain modified Y molecular sieves. The concentration of tetrapropylammonium hydroxide solution is 0.12mol / L, and the mass ratio of Y molecular sieve to water in the solution is 1:9.
[0063] Table 1 Main physicochemical properties of hydrocracking catalysts.
[0064]
[0065] Example 3
[0066] Using straight-run diesel as raw material, the upper bed of hydrocracking reactor is filled with catalyst , the lower bed is filled with catalyst , the catalyst loading volume ratio is 1:1.
PUM
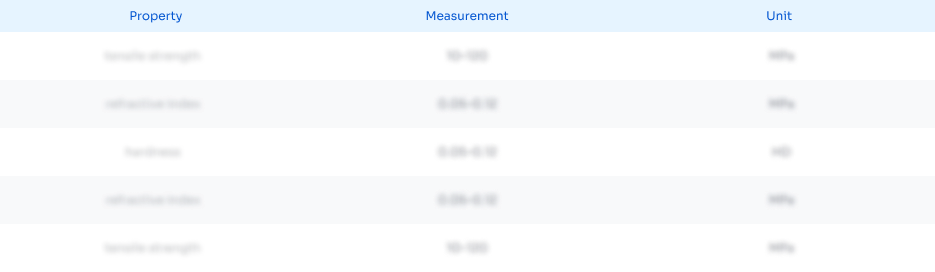
Abstract
Description
Claims
Application Information

- R&D Engineer
- R&D Manager
- IP Professional
- Industry Leading Data Capabilities
- Powerful AI technology
- Patent DNA Extraction
Browse by: Latest US Patents, China's latest patents, Technical Efficacy Thesaurus, Application Domain, Technology Topic, Popular Technical Reports.
© 2024 PatSnap. All rights reserved.Legal|Privacy policy|Modern Slavery Act Transparency Statement|Sitemap|About US| Contact US: help@patsnap.com