Ordered carbon-based composite electrode material and preparation method thereof
A composite electrode and ordered carbon technology, which is applied in the manufacture of hybrid capacitor electrodes and hybrid/electric double layer capacitors, can solve the problems of high cost, low efficiency and complicated methods, and achieves convenient operation, high efficiency and simple reaction control. Effect
- Summary
- Abstract
- Description
- Claims
- Application Information
AI Technical Summary
Problems solved by technology
Method used
Image
Examples
preparation example Construction
[0032] See figure 1 , a method for preparing an ordered carbon-based composite electrode material, comprising the following steps:
[0033] S1. Provide oriented composite conductive nanofiber film;
[0034] S2. Dry the oriented composite conductive nanofiber film for 24 hours, then raise the temperature to 250-350°C at a heating rate of 1-5°C / min for pre-oxidation, preferably at 2°C / min Raise the temperature to 280°C at the heating rate for pre-oxidation, and keep it at 280°C for 1 hour;
[0035] S3. Carbonize the pre-oxidized fiber membrane at a rate of 1-5°C / min to 1000-1200°C in a protective atmosphere to obtain the ordered carbon-based composite electrode material, preferably, In a high-purity nitrogen atmosphere, the temperature was raised to 1100 °C at a rate of 2 °C / min for carbonization, and kept at 1100 °C for 1 h.
[0036] In the preparation method, the oriented composite conductive nanofiber film is oriented carbon nanotube / polyacrylonitrile (SWNTs / PAN) composite...
Embodiment 1
[0039] The oriented porous graphene / polyacrylonitrile (Gr / PAN) composite conductive nanofiber membrane prepared by electrospinning was dried at room temperature for 24 h in an electric constant temperature drying oven, then taken out and placed in a muffle furnace at 2 °C / The heating rate of min was increased to 280°C for pre-oxidation, and the temperature was kept at 280°C for 1h. Then transfer to a tube furnace, in a high-purity nitrogen atmosphere, heat up to 1100° at a heating rate of 2°C / min for carbonization, and keep at 1100° for 1 hour to obtain an ordered carbon nanofiber / composite carbon nanofiber electrode Material. See Figures 2a to 2c , the figure shows the nanofibers obtained after carbonization treatment. It can be seen from the figure that the prepared C-Gr / PAN nanofiber electrode material has a high degree of orientation.
[0040] See image 3 , the Gr / PAN composite conductive nanofiber membrane of the present embodiment adopts an electrospinning device a...
Embodiment 2
[0046] Oriented magnetic nanometer ferroferric oxide / graphene / polyacrylonitrile (Fe 3 o 4 / Gr / PAN) composite conductive nanofiber membrane, placed in an electric constant temperature drying oven and dried at room temperature for 24 hours, taken out and placed in a muffle furnace to pre-oxidize at 280°C at a heating rate of 2°C / min, and then heated at 280°C Keep warm for 1h. Then transfer to a tube furnace, in a high-purity nitrogen atmosphere, heat up to 1100° at a heating rate of 2°C / min for carbonization, and keep at 1100° for 1 hour to obtain an ordered carbon nanofiber / composite carbon nanofiber electrode Material. See Figures 6a to 6c , the figure shows the nanofibers obtained after carbonization treatment. It can be seen from the figure that the prepared C-Fe 3 o 4 / Gr / PAN nanofiber electrode material has a high degree of orientation.
[0047] See Figure 7 , the Fe of this example 3 o 4 The / Gr / PAN composite conductive nanofiber membrane adopts the electrospin...
PUM
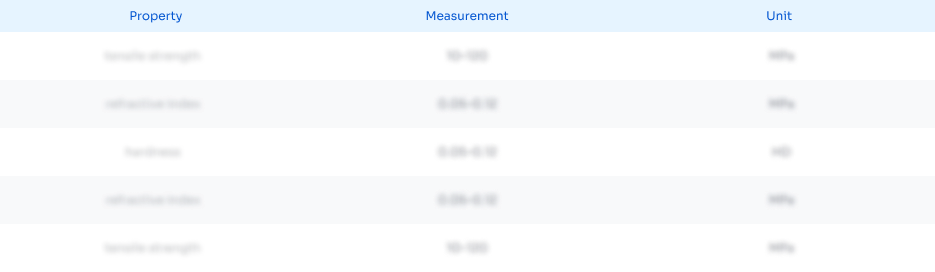
Abstract
Description
Claims
Application Information

- Generate Ideas
- Intellectual Property
- Life Sciences
- Materials
- Tech Scout
- Unparalleled Data Quality
- Higher Quality Content
- 60% Fewer Hallucinations
Browse by: Latest US Patents, China's latest patents, Technical Efficacy Thesaurus, Application Domain, Technology Topic, Popular Technical Reports.
© 2025 PatSnap. All rights reserved.Legal|Privacy policy|Modern Slavery Act Transparency Statement|Sitemap|About US| Contact US: help@patsnap.com