Composition for manufacturing diaphragm of lithium battery
A lithium battery diaphragm and composition technology, which is applied in the direction of battery pack parts, circuits, electrical components, etc., can solve the problems that the diaphragm cannot meet the needs of power batteries, high longitudinal shrinkage, uneven hole formation, etc., to achieve low cost, High porosity and uniform pore formation
- Summary
- Abstract
- Description
- Claims
- Application Information
AI Technical Summary
Problems solved by technology
Method used
Image
Examples
Embodiment 1
[0012] Materials:
[0013] 10Kg polyethylene powder and 10Kg paraffin oil (the mixing ratio of polyethylene powder and paraffin oil is 1:1)
[0014] 10Kg polyethylene powder comprises the polyethylene particle of the antioxidant 1010 of 0.1Kg, the antioxidant 1076 of 0.1Kg and 9.8Kg (the quality of described antioxidant a, antioxidant b accounts for total polyethylene powder respectively 1% of the mass), the polyethylene particles are high-density polyethylene, and its molecular weight is 300,000.
[0015] Step 1. Put the polyethylene powder added with antioxidant into the extruder, melt it at 250°C, and add paraffin oil during the melting process;
[0016] Step 2. The liquid after mixing polyethylene powder and paraffin oil is extruded with a twin-screw extruder, and the extruded liquid is rapidly cooled to a temperature of 50°C to form an oil film;
[0017] Step 3. The cooled oil film is stretched longitudinally in 7 stages on stretching rollers at 110°C, the stretching ra...
Embodiment 2
[0023] Materials:
[0024] 10Kg polyethylene powder and 12.5Kg paraffin oil (the mixing ratio of polyethylene powder and paraffin oil is 0.8)
[0025] 10Kg polyethylene powder comprises the polyethylene particle of the antioxidant 168 of 0.78Kg, the antioxidant 264 of 0.78Kg and 8.44Kg (the quality of described antioxidant a, antioxidant b accounts for total polyethylene powder respectively 7.8% of the mass), the polyethylene particles are high-density polyethylene, and its molecular weight is 450,000.
[0026] Step 1. Put the polyethylene powder added with antioxidant into the extruder, melt it at 250°C, and add paraffin oil during the melting process;
[0027] Step 2. The liquid after mixing polyethylene powder and paraffin oil is extruded with a twin-screw extruder, and the extruded liquid is rapidly cooled to a temperature of 50°C to form an oil film;
[0028] Step 3. The cooled oil film is stretched longitudinally in 7 stages on stretching rollers at 110°C, the stretchi...
Embodiment 3
[0034] Materials:
[0035] 10Kg polyethylene powder and 28.46Kg paraffin oil (the mixing ratio of polyethylene powder and paraffin oil is 26:74)
[0036] 10Kg polyethylene powder comprises the polyethylene particle of the antioxidant 168 of 0.55Kg, the antioxidant 264 of 0.55Kg and 8.9Kg (the quality of described antioxidant a, antioxidant b accounts for total polyethylene powder respectively 5.5% of the mass), the polyethylene particles are high-density polyethylene, and its molecular weight is 600,000.
[0037] Step 1. Put the polyethylene powder added with antioxidant into the extruder, melt it at 250°C, and add paraffin oil during the melting process;
[0038] Step 2. The liquid after mixing polyethylene powder and paraffin oil is extruded with a twin-screw extruder, and the extruded liquid is rapidly cooled to a temperature of 50°C to form an oil film;
[0039] Step 3. The cooled oil film is stretched longitudinally in 7 stages on stretching rollers at 110°C, the stretc...
PUM
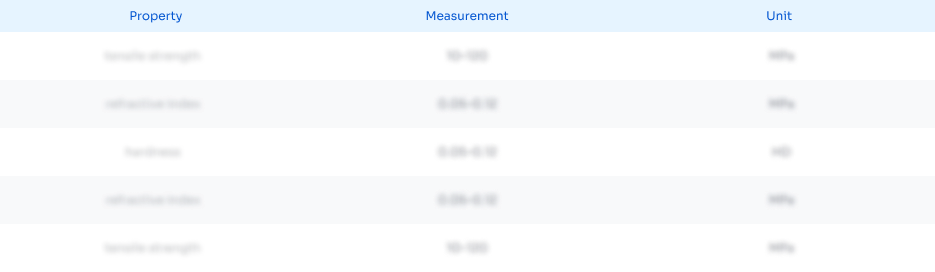
Abstract
Description
Claims
Application Information

- R&D
- Intellectual Property
- Life Sciences
- Materials
- Tech Scout
- Unparalleled Data Quality
- Higher Quality Content
- 60% Fewer Hallucinations
Browse by: Latest US Patents, China's latest patents, Technical Efficacy Thesaurus, Application Domain, Technology Topic, Popular Technical Reports.
© 2025 PatSnap. All rights reserved.Legal|Privacy policy|Modern Slavery Act Transparency Statement|Sitemap|About US| Contact US: help@patsnap.com