Conversion flange forge piece forging and thermal treatment technology
A technology for converting flanges and forging heating, which is applied in the direction of manufacturing tools, metal processing equipment, forging/pressing/hammer devices, etc. It can solve the problems of short service life and high forging cost, so as to improve service life and reduce corrosion resistance , the effect of grain refinement
- Summary
- Abstract
- Description
- Claims
- Application Information
AI Technical Summary
Problems solved by technology
Method used
Image
Examples
Embodiment 1
[0057] Embodiment 1: In the embodiment,
[0058] Step 1. Melting the raw materials to obtain smelted steel ingots. Specifically, step 1 includes:
[0059] (1) Carry out EF+LF+VD treatment process on raw materials.
[0060] (2) Next, perform ESR processing.
[0061] Step 2, forging and heating. The furnace charging temperature before the ingot is heated for forging is 650°C. Specifically, step 2 includes:
[0062] (1) Heating; the heating temperature is 1200°C.
[0063] (2) heat preservation; at this time, the thickness of the steel ingot is 800mm, and the heat preservation time is 10 hours.
[0064] Step 3, forging; the forging process includes three fire times.
[0065] (1) First firing: the forging temperature is 1200°C. In the first firing, the steel ingot is drawn, upset and re-drawn in sequence, and the total drawing ratio is 4.3; the upsetting ratio is 2.6. The final forging temperature is 850°C.
[0066] After finishing the first firing, the steel ingot is put...
Embodiment 2
[0079] Step 1. Melting the raw materials to obtain smelted steel ingots. Specifically, step 1 includes:
[0080] (1) Carry out EF+LF+VD treatment process on raw materials.
[0081] (2) Next, perform ESR processing.
[0082] Step 2, forging and heating. The furnace charging temperature before the ingot is heated for forging is 650°C. Specifically, step 2 includes:
[0083] (1) Heating; the heating temperature is 1220°C.
[0084] (2) heat preservation; at this time, the thickness of the steel ingot is 800mm, and the heat preservation time is 11 hours.
[0085] Step 3, forging; the forging process includes three fire times.
[0086] (1) First firing: the forging temperature is 1200°C. In the first firing, the steel ingot is drawn, upset and re-drawn in sequence, wherein the total drawing ratio is 4.5; the upsetting ratio is 2.5. The final forging temperature is 900°C.
[0087] After finishing the first firing, the steel ingot is put into the forging heating furnace for h...
Embodiment 3
[0100] Step 1. Melting the raw materials to obtain smelted steel ingots. Specifically, step 1 includes:
[0101] (1) Carry out EF+LF+VD treatment process on raw materials.
[0102] (2) Next, perform ESR processing.
[0103] Step 2, forging and heating. The furnace charging temperature before the steel ingot is forged and heated is 500°C. Specifically, step 2 includes:
[0104] (1) Heating; the heating temperature is 1240°C.
[0105] (2) heat preservation; at this time, the thickness of the steel ingot is 800, and the heat preservation time is 10.5h.
[0106] Step 3, forging; the forging process includes three fire times.
[0107] (1) First firing: the forging temperature is 1200°C. In the first firing, the steel ingot is drawn, upset and re-drawn in sequence, and the total drawing ratio is 4.1; the upsetting ratio is 2.3. The final forging temperature is 950°C.
[0108] After finishing the first firing, the steel ingot is put into the forging heating furnace for heating...
PUM
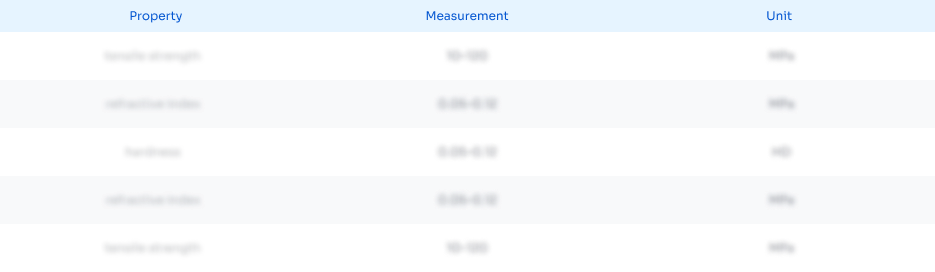
Abstract
Description
Claims
Application Information

- Generate Ideas
- Intellectual Property
- Life Sciences
- Materials
- Tech Scout
- Unparalleled Data Quality
- Higher Quality Content
- 60% Fewer Hallucinations
Browse by: Latest US Patents, China's latest patents, Technical Efficacy Thesaurus, Application Domain, Technology Topic, Popular Technical Reports.
© 2025 PatSnap. All rights reserved.Legal|Privacy policy|Modern Slavery Act Transparency Statement|Sitemap|About US| Contact US: help@patsnap.com