Laser cladding method and device for metal round rod surface
A technology of laser cladding and round rods, which is applied in the coating process of metal materials, coating, etc., can solve the problems that cannot really meet the requirements of the cladding parts, poor performance of joint parts, waste of precious powder, etc., and achieve simple structure , cladding time is short, the effect of reducing the generation of pores
- Summary
- Abstract
- Description
- Claims
- Application Information
AI Technical Summary
Problems solved by technology
Method used
Image
Examples
Embodiment 1
[0028] A method for laser cladding on the surface of a metal round rod, specifically: prepare a laser, the laser cladding nozzle of the laser is located on the outer peripheral surface near the end of the metal round rod, the position of the laser cladding nozzle is fixed, and the metal The round bar can not only rotate at a constant speed but also move at a constant speed along the axial direction at the same time, so that the movement track of the laser cladding nozzle relative to the metal round bar is a helical line along the surface of the metal round bar, that is, it moves forward while rotating with the metal round bar. , from a perspective, the surface of the metal rod will form a number of cladding rings that are closely connected and have a certain angle.
[0029] In order to further improve the cladding efficiency, the nozzle of the laser cladding nozzle in this method has a flat rectangular opening structure, and the long side of the rectangular opening structure is...
Embodiment 2
[0032] Such as figure 1 As shown, a metal round rod surface laser cladding device is provided, which includes a laser (only the laser cladding nozzle 1 is shown) and a rotating motor 3 that can drive the metal round rod 2 to rotate at a uniform speed. The first ends of the rods 2 are connected by a connecting device 4, and a support platform 5 adapted to the outer peripheral surface of the metal round rods is provided under the second ends of the metal round rods 2 to support the metal round rods 2 in a horizontal arrangement; the laser of the laser The cladding nozzle 1 is located near the outer peripheral surface of either end of the metal round rod 2; it also includes a linear sliding mechanism 6 arranged below the metal round rod 2 and parallel to the axis of the metal round rod, and the support table 5 and the rotating motor 3 are both provided On the linear sliding mechanism 6, the linear sliding mechanism 6 can drive the metal round rod 2 to move at a constant speed in ...
Embodiment 3
[0048] The difference between this embodiment and Embodiment 2 is that the high temperature resistant baffle is set horizontally, which can also collect excess powder and realize immediate reuse.
PUM
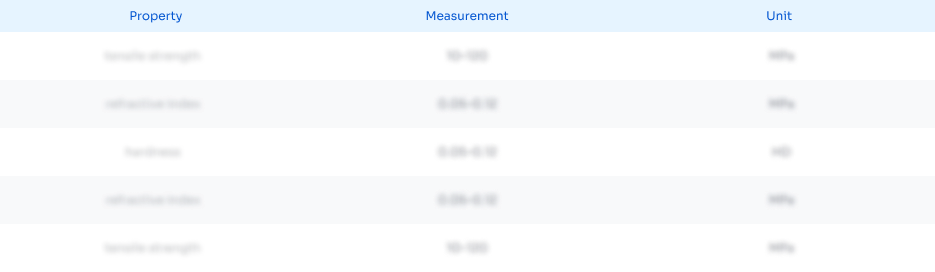
Abstract
Description
Claims
Application Information

- Generate Ideas
- Intellectual Property
- Life Sciences
- Materials
- Tech Scout
- Unparalleled Data Quality
- Higher Quality Content
- 60% Fewer Hallucinations
Browse by: Latest US Patents, China's latest patents, Technical Efficacy Thesaurus, Application Domain, Technology Topic, Popular Technical Reports.
© 2025 PatSnap. All rights reserved.Legal|Privacy policy|Modern Slavery Act Transparency Statement|Sitemap|About US| Contact US: help@patsnap.com