Liquid-liquid extraction-azeotropic rectification mixing process for separating propylene glycol monomethyl ether and water
A technology of propylene glycol methyl ether and azeotropic distillation, which is applied in ether separation/purification, ether preparation, organic chemistry, etc. It can solve the problems of complex operation, separation and purification without other mixtures, and inability to achieve efficient separation, so as to solve the problem of separation difficult effect
- Summary
- Abstract
- Description
- Claims
- Application Information
AI Technical Summary
Problems solved by technology
Method used
Image
Examples
Embodiment 1
[0032] The feed temperature is 45° C., the flow rate is 1000 kmol / h, and the pressure is 1 atm absolute pressure. The feed contains 92.2 mol% of propylene glycol methyl ether and 7.8 mol% of water. The theoretical plate number of the liquid-liquid extraction tower is 15, the feeding position of the propylene glycol methyl ether-water mixture is the 15th block, the feeding position of the extractant is the 1st block, the theoretical plate number of the azeotropic distillation column is 22, and the feeding position is Be the 11th piece, the theoretical plate number of recovery tower is 13 pieces, the 8th piece of feeding position, the flow rate of extraction agent is 250kmol / h (solvent ratio is 0.25), the volume of 2-ethylhexanoic acid and chloroform in the mixed extraction agent The molar mass ratio of the propylene glycol methyl ether after separation is 0.4, and the purity of the separated propylene glycol methyl ether is 99.90% (mol fraction), and the purity of water is 99.92...
Embodiment 2
[0034] The feed temperature is 45° C., the flow rate is 1000 kmol / h, and the pressure is 1 atm absolute pressure. The feed contains 92.2 mol% of propylene glycol methyl ether and 7.8 mol% of water. The number of theoretical plates of the liquid-liquid extraction tower is 13, the feeding position of the propylene glycol methyl ether-water mixture is the 13th, the feeding position of the extractant is the 1st block, the number of theoretical plates of the azeotropic distillation column is 20, and the feeding position is the 1st 9 blocks, the theoretical plate number of the recovery tower is 11 blocks, the 7th block of the feed position, the flow rate of the extractant is 400kmol / h (solvent ratio is 0.4), the mole of 2-ethylhexanoic acid and chloroform in the mixed extractant The mass ratio is 0.5, the purity of the separated propylene glycol methyl ether is 99.92% (mol fraction), and the purity of water is 99.91% (mol fraction).
Embodiment 3
[0036] The feed temperature is 45° C., the flow rate is 1000 kmol / h, and the pressure is 1 atm absolute pressure. The feed contains 92.2 mol% of propylene glycol methyl ether and 7.8 mol% of water. The number of theoretical plates of the liquid-liquid extraction tower is 11, the feed position of the propylene glycol methyl ether-water mixture is the 11th block, the feed position of the extractant is the 1st block, the number of theoretical plates of the azeotropic distillation column is 18, and the feed position is Be the 10th piece, the theoretical plate number of recovery tower is 10 pieces, the 6th piece of feed position, the flow rate of extraction agent is 500kmol / h (solvent ratio is 0.5), the 2-ethylhexanoic acid and chloroform in the mixed extraction agent The molar mass ratio of the propylene glycol methyl ether after separation is 0.55, and the purity of the separated propylene glycol methyl ether is 99.99% (mol fraction), and the purity of water is 99.94% (mol fractio...
PUM
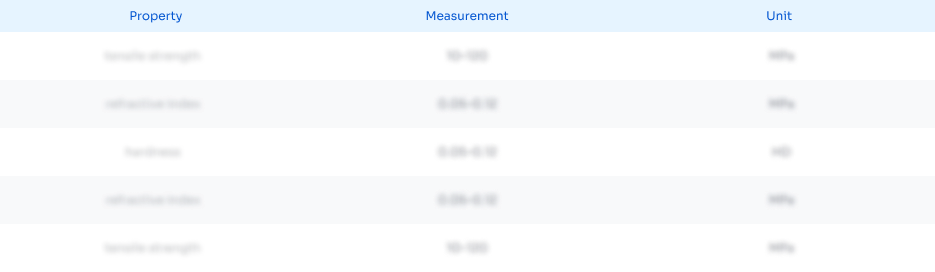
Abstract
Description
Claims
Application Information

- Generate Ideas
- Intellectual Property
- Life Sciences
- Materials
- Tech Scout
- Unparalleled Data Quality
- Higher Quality Content
- 60% Fewer Hallucinations
Browse by: Latest US Patents, China's latest patents, Technical Efficacy Thesaurus, Application Domain, Technology Topic, Popular Technical Reports.
© 2025 PatSnap. All rights reserved.Legal|Privacy policy|Modern Slavery Act Transparency Statement|Sitemap|About US| Contact US: help@patsnap.com