Preparation method of monolithic microporous-macroporous Silicalite-1@SiO2
A monolithic, microporous technology used in chemical instruments and methods, other chemical processes, etc.
- Summary
- Abstract
- Description
- Claims
- Application Information
AI Technical Summary
Problems solved by technology
Method used
Examples
Embodiment 1
[0020] A monolithic microporous-macroporous Silicalite-1@SiO 2 The preparation method comprises the following steps: 20 parts of epoxy resin, 25 parts of polyethylene glycol 1000 and 7 parts of polyethylene glycol 20000 are placed in a beaker, mixed, heated and melted, and when the solution is uniform and transparent, quickly add 15 parts of Triethylenetetramine, maintain the system temperature at 65°C and continuously stir vigorously for 25min, transfer the liquid in the beaker to the mold, react at 65°C for 3.5h, the liquid in the mold turns into a white solid, put the white solid in distilled water Soak to remove polyethylene glycol, and finally dry naturally at room temperature to obtain a monolithic epoxy resin macroporous polymer with a three-dimensional skeleton structure; after vacuum drying the polymer template prepared above at 50 ° C for 3.5 h, in Soak in tetraethyl orthosilicate for 48h, then take out the material and place it in NH at 25°C 3 In the atmosphere for...
Embodiment 2
[0022] A monolithic microporous-macroporous Silicalite-1@SiO 2 The preparation method comprises the following steps: 15 parts of epoxy resin, 20 parts of polyethylene glycol 1000 and 5 parts of polyethylene glycol 20000 are placed in a beaker, mixed, heated and melted, and when the solution is uniform and transparent, quickly add 10 parts of Triethylenetetramine, maintain the system temperature at 64°C and continuously stir vigorously for 20 minutes, transfer the liquid in the beaker to the mold, react at 64°C for 3 hours, the liquid in the mold turns into a white solid, soak the white solid in distilled water to remove polyethylene glycol, and finally dry naturally at room temperature to obtain a monolithic epoxy resin macroporous polymer with a three-dimensional skeleton structure; after vacuum drying the polymer template prepared above at 45°C for 3 h, Soak in tetraethyl acetate for 47h, then take out the material and place it in NH at 20°C 3 In the atmosphere for 25h and ...
Embodiment 3
[0024] A monolithic microporous-macroporous Silicalite-1@SiO 2 The preparation method comprises the following steps: 25 parts of epoxy resin, 30 parts of polyethylene glycol 1000 and 9 parts of polyethylene glycol 20000 are placed in a beaker, mixed, heated and melted, and when the solution is uniform and transparent, quickly add 20 parts of Triethylenetetramine, maintain the system temperature at 66°C and continuously stir vigorously for 30 minutes, transfer the liquid in the beaker to the mold, react at 66°C for 4 hours, the liquid in the mold turns into a white solid, soak the white solid in distilled water to remove polyethylene glycol, and finally dry naturally at room temperature to obtain a monolithic epoxy resin macroporous polymer with a three-dimensional skeleton structure; the polymer template prepared above was vacuum-dried at 55°C for 4 hours, and then placed on orthosilicon Soak in tetraethyl acetate for 49h, then take out the material and place it in NH at 30°C ...
PUM
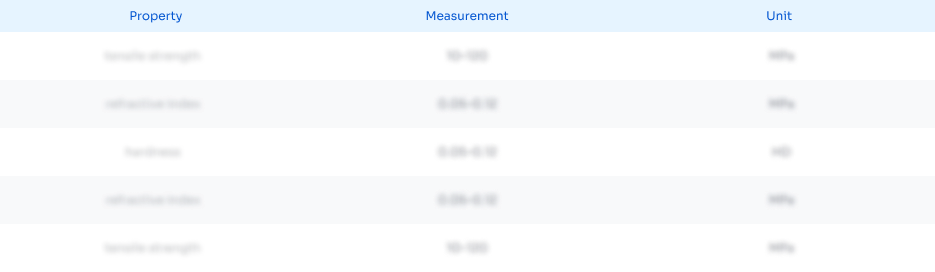
Abstract
Description
Claims
Application Information

- R&D Engineer
- R&D Manager
- IP Professional
- Industry Leading Data Capabilities
- Powerful AI technology
- Patent DNA Extraction
Browse by: Latest US Patents, China's latest patents, Technical Efficacy Thesaurus, Application Domain, Technology Topic, Popular Technical Reports.
© 2024 PatSnap. All rights reserved.Legal|Privacy policy|Modern Slavery Act Transparency Statement|Sitemap|About US| Contact US: help@patsnap.com