Exhaust gas treatment device and exhaust gas treatment method for exhaust gas from magnet sintering
A waste gas treatment device and waste gas technology, which are applied in the field of waste gas treatment devices and waste gas treatment devices, can solve the problems of poor purification effect of waste gas devices, and achieve the effects of saving resources, convenient use and prolonging service life.
- Summary
- Abstract
- Description
- Claims
- Application Information
AI Technical Summary
Problems solved by technology
Method used
Image
Examples
Embodiment 1
[0066] see figure 1 , The waste gas treatment device for waste gas from magnet sintering in this embodiment includes a spray bin 1 , a drug delivery mechanism, a heat recovery mechanism, a dust removal mechanism, an exhaust gas purification mechanism, an air inlet valve 4 , a water inlet valve 14 , and a controller 6 .
[0067] The spray chamber 1 is used to spray and purify the exhaust gas. An atomizing nozzle 7 for spraying is set in the spray chamber 1 of the waste gas by using water, and the spray chamber 1 is connected to a spray chamber 1 for discharge. The drainpipe 9 for accumulated water, the top of the spray chamber 1 is also connected to one end of an exhaust pipe 8, after the waste gas flows into the spray chamber 1, the atomizing nozzle 7 sprays the raw water, and the spray chamber 1 The waste gas is purified, and the raw water forms waste water after dissolving the soluble harmful substances in the waste gas. The waste water flows out from the drain pipe 9, and t...
Embodiment 2
[0088] see image 3The difference between the exhaust gas treatment device of this embodiment and the exhaust gas treatment device of Embodiment 1 is that the exhaust gas treatment device of this embodiment has two exhaust gas purification bins 12, and one side of the two exhaust gas purification bins 12 is respectively connected by an outlet valve 16. Exhaust pipe 8 has also increased water outlet valve 10 and water level detector 11 in addition.
[0089] The water outlet valve 10 is arranged on the drain pipe 9 and is used for opening and closing the drain pipe 9 .
[0090] The water level detector 11 is arranged in the spray chamber 1 and is used for detecting the water level value of the accumulated water in the spray chamber 1 .
[0091] According to the water level value detected by the water level detector 11, the controller 6 controls the water outlet valve 10 to open when the water level value is not less than a preset high water level value; otherwise, the controlle...
PUM
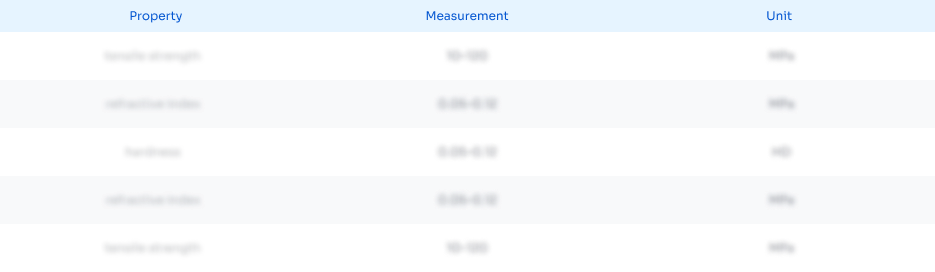
Abstract
Description
Claims
Application Information

- R&D
- Intellectual Property
- Life Sciences
- Materials
- Tech Scout
- Unparalleled Data Quality
- Higher Quality Content
- 60% Fewer Hallucinations
Browse by: Latest US Patents, China's latest patents, Technical Efficacy Thesaurus, Application Domain, Technology Topic, Popular Technical Reports.
© 2025 PatSnap. All rights reserved.Legal|Privacy policy|Modern Slavery Act Transparency Statement|Sitemap|About US| Contact US: help@patsnap.com