Polishing solution for stainless steel processing and preparation method of polishing solution
A technology of polishing liquid and stainless steel, applied in polishing compositions containing abrasives, etc., can solve the problems of high raw material cost, complicated preparation method, unsuitable for industrialized popularization and production, etc., and achieves low surface roughness, simple method and good cooling. effect of effect
- Summary
- Abstract
- Description
- Claims
- Application Information
AI Technical Summary
Problems solved by technology
Method used
Examples
Embodiment 1
[0032] A polishing solution for stainless steel processing, comprising the following raw materials in parts by weight: 12 parts of sulfated castor oil, 11 parts of cocamidopropyl amine oxide, 23 parts of modified silicon dioxide, 11 parts of ethyl silicone oil, and 14 parts of abrasive , 9 parts of silica sol, 6 parts of brightener, 9 parts of compound additive, 13 parts of decaglycerol decaoleate, 9 parts of ethanol solution, 8 parts of surfactant, 5 parts of pH regulator, 9 parts of corrosion inhibitor parts and 20 parts of deionized water.
[0033] A preparation method of a polishing liquid for stainless steel processing, comprising the following preparation steps:
[0034] a. Mix the abrasive, decaglycerol decaoleate and ethanol solution into the reaction kettle, raise the temperature to 65°C, heat the reaction for 20 minutes, then cool to room temperature, then add the surfactant, and carry out ultrasonic dispersion treatment for 15 minutes to obtain a mixture ;
[0035...
Embodiment 2
[0045] A polishing liquid for stainless steel processing, comprising the following raw materials in parts by weight: 11 parts of sulfated castor oil, 11 parts of cocamidopropyl amine oxide, 22 parts of modified silicon dioxide, 11 parts of ethyl silicone oil, and 15 parts of abrasive , 11 parts of silica sol, 6 parts of brightener, 15 parts of compound additive, 13 parts of deca-polyglycerol decaoleate, 9 parts of ethanol solution, 5 parts of surfactant, 6 parts of pH regulator, 7 parts of corrosion inhibitor parts and 20 parts of deionized water.
[0046] A preparation method of a polishing liquid for stainless steel processing, comprising the following preparation steps:
[0047] a. Mix the abrasive, decaglycerol decaoleate and ethanol solution into the reaction kettle, raise the temperature to 68°C, heat the reaction for 24 minutes, then cool to room temperature, then add the surfactant, and carry out ultrasonic dispersion treatment for 18 minutes to obtain a mixture ;
...
Embodiment 3
[0058] A polishing liquid for stainless steel processing, comprising the following raw materials in parts by weight: 10 parts of sulfated castor oil, 11 parts of cocamidopropyl amine oxide, 21 parts of modified silicon dioxide, 12 parts of ethyl silicone oil, and 16 parts of abrasive , 12 parts of silica sol, 8 parts of brightener, 13 parts of compound additive, 12 parts of deca-polyglycerol decaoleate, 8 parts of ethanol solution, 6 parts of surfactant, 7 parts of pH regulator, 7 parts of corrosion inhibitor parts and 25 parts of deionized water.
[0059] A preparation method of a polishing liquid for stainless steel processing, comprising the following preparation steps:
[0060] a. Mix the abrasive, decaglycerol decaoleate and ethanol solution into the reaction kettle, raise the temperature to 65°C, heat and react for 24 minutes, then cool to room temperature, then add a surfactant, perform ultrasonic dispersion treatment for 18 minutes, and obtain a mixture ;
[0061] b....
PUM
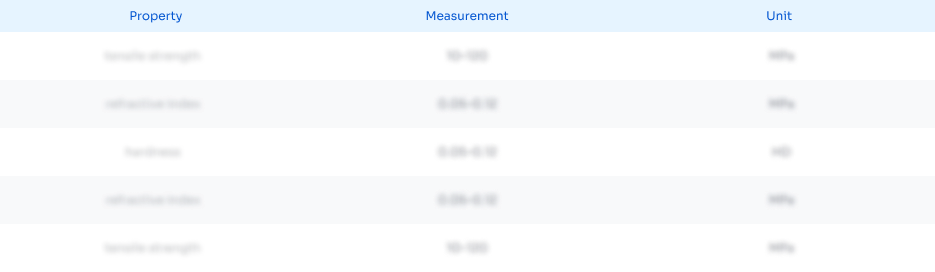
Abstract
Description
Claims
Application Information

- R&D Engineer
- R&D Manager
- IP Professional
- Industry Leading Data Capabilities
- Powerful AI technology
- Patent DNA Extraction
Browse by: Latest US Patents, China's latest patents, Technical Efficacy Thesaurus, Application Domain, Technology Topic, Popular Technical Reports.
© 2024 PatSnap. All rights reserved.Legal|Privacy policy|Modern Slavery Act Transparency Statement|Sitemap|About US| Contact US: help@patsnap.com