Method of preparing high-efficiency photocatalytic composite material
A composite material and photocatalytic technology, which is applied in the field of preparation of high-efficiency photocatalytic composite materials, can solve the problems of no adsorption performance, no firm fixation, large pores between fibers, etc., to avoid a large number of shedding, improve mechanical properties, and improve adsorption performance effect
- Summary
- Abstract
- Description
- Claims
- Application Information
AI Technical Summary
Problems solved by technology
Method used
Image
Examples
Embodiment 1
[0029] 1. Tryptone, yeast powder and mannitol are configured nutrient solution according to mass ratio 4.5:3:25.5; 2 ) in nano-TiO with a concentration of 1g / L 2 Immerse in the suspension for 60min.
[0030] 2. Pour 180mL of nutrient solution and soaked sample into a 500mL Erlenmeyer flask, seal and sterilize in an autoclave at 126°C and 0.15MP for 1 hour.
[0031] 3. In the biological safety cabinet, use a pipette gun to pipette 10mL of the original bacterial solution into the cooled nutrient solution. Then, the inoculated nutrient solution was placed in a shaker incubator for static culture for 4 days.
[0032] 4. Take out the cultured composite bacterial cellulose, wash it with deionized water, put it into 0.11mol / L NaOH solution, and boil it in alkali for 10 hours in a water bath at 80°C to remove residual culture medium and bacteria. After the alkali boiling is finished, the bacterial cellulose is rinsed again with deionized water until it becomes neutral, and then put...
Embodiment 2
[0035] 1. Tryptone, yeast powder and mannitol are configured nutrient solution according to mass ratio 4.5:3:25.5; 2 ) at a concentration of 2g / L nano-TiO 2 Immerse in the suspension for 30min.
[0036] 2. Pour 180mL of nutrient solution and soaked sample into a 500mL Erlenmeyer flask, seal and sterilize in an autoclave at 126°C and 0.15MP for 1 hour.
[0037] 3. In the biological safety cabinet, use a pipette gun to pipette 10mL of the original bacterial solution into the cooled nutrient solution. Then, the inoculated nutrient solution was placed in a shaker incubator for static culture for 3 days.
[0038] 4. Take out the cultured composite bacterial cellulose, wash it with deionized water, put it into 0.11mol / L NaOH solution, and boil it in alkali for 12 hours in a water bath at 80°C to remove residual culture medium and bacteria. After the alkali boiling, the bacterial cellulose was rinsed again with deionized water until it became neutral, and then put into 80° C. deioni...
Embodiment 3
[0041] 1. Tryptone, yeast powder and mannitol are configured nutrient solution according to mass ratio 4.5:3:25.5; 2 ) in nano-TiO with a concentration of 1g / L 2 Immerse in the suspension for 30min.
[0042] 2. Pour 180mL of nutrient solution and soaked sample into a 500mL Erlenmeyer flask, seal and sterilize in an autoclave at 126°C and 0.15MP for 1 hour.
[0043] 3. In the biological safety cabinet, use a pipette gun to pipette 10mL of the original bacterial solution into the cooled nutrient solution. Then, the inoculated nutrient solution was placed in a shaker incubator for static culture for 5 days.
[0044] 4. Take out the cultured composite bacterial cellulose, wash it with deionized water, put it into 0.11mol / L NaOH solution, and boil it in alkali for 8 hours in a water bath at 80°C to remove residual culture medium and bacteria. After the alkali boiling, the bacterial cellulose was rinsed again with deionized water to neutrality, and put into deionized water at 80°...
PUM
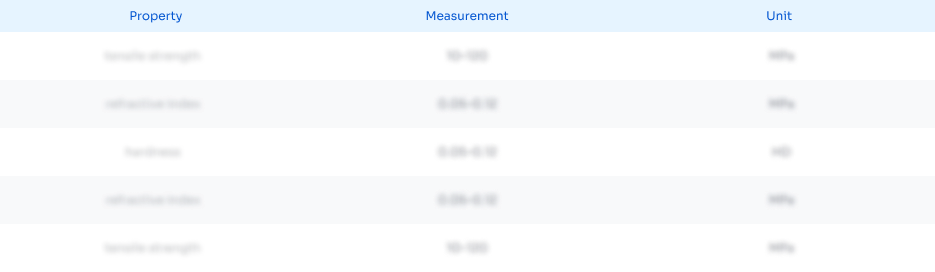
Abstract
Description
Claims
Application Information

- Generate Ideas
- Intellectual Property
- Life Sciences
- Materials
- Tech Scout
- Unparalleled Data Quality
- Higher Quality Content
- 60% Fewer Hallucinations
Browse by: Latest US Patents, China's latest patents, Technical Efficacy Thesaurus, Application Domain, Technology Topic, Popular Technical Reports.
© 2025 PatSnap. All rights reserved.Legal|Privacy policy|Modern Slavery Act Transparency Statement|Sitemap|About US| Contact US: help@patsnap.com