Oriented full-thickness cartilage scaffold containing calcified layer and preparation method thereof
A calcified layer and orientation technology, applied in the fields of biomaterials and biomedical engineering, can solve problems such as cartilage and bone microenvironment disorders, and achieve the effect of promoting differentiation
- Summary
- Abstract
- Description
- Claims
- Application Information
AI Technical Summary
Problems solved by technology
Method used
Examples
Embodiment 1
[0013] 1) Prepare 0.3 mL of a mixed solution of silk fibroin and nano-hydroxyapatite hexafluoroisopropanol with a concentration of 12% and a mass ratio of 1:1, pour it into a mold, and dry it at room temperature to obtain a calcified bottom bracket;
[0014] 2) Prepare a compound solution with a total concentration of 4% according to the mass ratio of decellularized cartilage extracellular matrix and silk fibroin protein at 1:1. After mixing well, take 1 mL of the compound solution and add it to the surface of the calcified layer scaffold, and quickly carry out at -20°C. Gradient cooling to prepare oriented decellularized cartilage extracellular matrix and silk fibroin oriented upper layer scaffold. Finally, the whole scaffold was freeze-dried, treated with ethanol, and then freeze-dried for 48 hours to obtain the oriented full-thickness cartilage scaffold containing the calcified layer.
Embodiment 2
[0016] 1) Prepare 0.4 mL of a mixed solution of silk fibroin and β-tricalcium phosphate hexafluoroisopropanol with a concentration of 15% and a mass ratio of 1:1, pour it into a mold, and dry it at room temperature to obtain a calcified underlying scaffold;
[0017] 2) Prepare a compound solution with a total concentration of 5% according to the mass ratio of decellularized cartilage extracellular matrix and silk fibroin protein at 1:1. After mixing thoroughly, take 1 mL of the compound solution and add it to the surface of the calcified layer scaffold, and quickly carry out at -20 ° C. Gradient cooling to prepare oriented decellularized cartilage extracellular matrix and silk fibroin oriented upper layer scaffold. Finally, the whole scaffold was freeze-dried, treated with ethanol, and then freeze-dried for 48 hours to obtain the oriented full-thickness cartilage scaffold containing the calcified layer.
Embodiment 3
[0019] 1) 0.5 mL of a mixed solution of silk fibroin and bioactive glass hexafluoroisopropanol with a concentration of 20% and a mass ratio of 1:1 was prepared, and poured into a mold, and dried at room temperature to obtain a calcified underlying scaffold;
[0020] 2) Prepare a compound solution with a total concentration of 6% according to the mass ratio of the decellularized cartilage extracellular matrix and silk fibroin protein at a ratio of 1:1. After mixing thoroughly, take 1 mL of the compound solution and add it to the surface of the calcified layer scaffold, and quickly carry out at -20°C. Gradient cooling to prepare oriented decellularized cartilage extracellular matrix and silk fibroin oriented upper layer scaffold. Finally, the whole scaffold was freeze-dried, treated with ethanol, and then freeze-dried for 48 hours to obtain the oriented full-thickness cartilage scaffold containing the calcified layer.
PUM
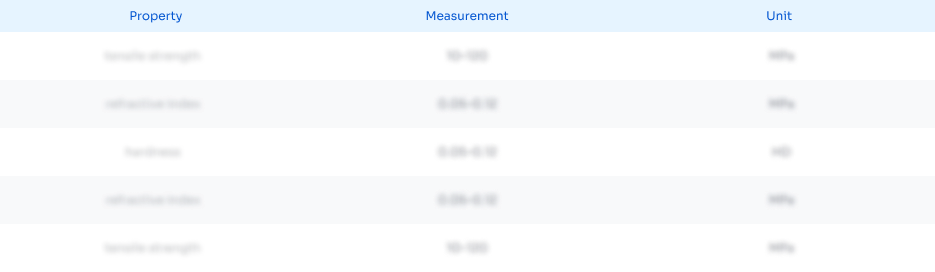
Abstract
Description
Claims
Application Information

- R&D Engineer
- R&D Manager
- IP Professional
- Industry Leading Data Capabilities
- Powerful AI technology
- Patent DNA Extraction
Browse by: Latest US Patents, China's latest patents, Technical Efficacy Thesaurus, Application Domain, Technology Topic, Popular Technical Reports.
© 2024 PatSnap. All rights reserved.Legal|Privacy policy|Modern Slavery Act Transparency Statement|Sitemap|About US| Contact US: help@patsnap.com