Vent plug for ventilation and stirring of bottom of smelting furnace and metal smelting furnace
A technology of ventilating stirring and venting plugs, which is applied in the direction of stirring devices, furnaces, furnace materials, etc., can solve the problems of high operating costs, surrounding environmental pollution, and discharge of fluorine-containing solids, and achieves reasonable fixed installation structure, anti-metal liquid penetration, The effect of preventing the breathable core from coming out
- Summary
- Abstract
- Description
- Claims
- Application Information
AI Technical Summary
Problems solved by technology
Method used
Image
Examples
Embodiment Construction
[0040] In order to better explain the present invention and facilitate understanding, the present invention will be described in detail below in conjunction with the accompanying drawings.
[0041] see figure 1 Shown is a schematic diagram of the structure of a vent plug 100 in a preferred embodiment of the present invention. The vent plug 100 is used to be installed at the bottom of the furnace body of the smelting furnace. Tiny bubbles of gas, agitated and refined simultaneously by aeration. The venting plug 100 includes a ventilating core 2 , a high temperature resistant seamless pipe 6 , a first cured refractory castable structure 7 and a second cured refractory castable structure 1 . The air-permeable core 2 is made of calcined corundum particles with a particle size of 0.5-1mm, which is modified by micron and sub-nanometer alumina-silica sol-gel surfaces (ceramic sintered on the surface of refractory corundum particles at high temperature) Uniformly coated with micron ...
PUM
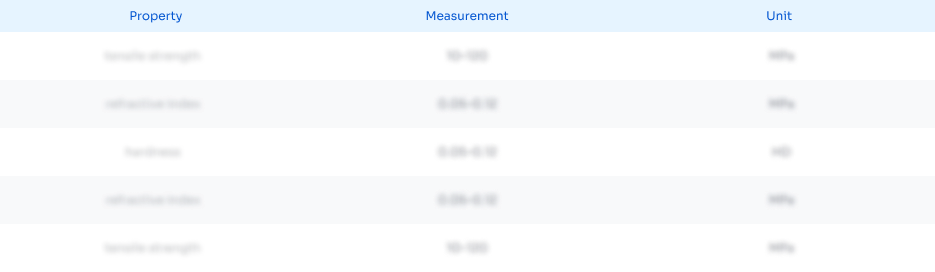
Abstract
Description
Claims
Application Information

- Generate Ideas
- Intellectual Property
- Life Sciences
- Materials
- Tech Scout
- Unparalleled Data Quality
- Higher Quality Content
- 60% Fewer Hallucinations
Browse by: Latest US Patents, China's latest patents, Technical Efficacy Thesaurus, Application Domain, Technology Topic, Popular Technical Reports.
© 2025 PatSnap. All rights reserved.Legal|Privacy policy|Modern Slavery Act Transparency Statement|Sitemap|About US| Contact US: help@patsnap.com