A high temperature steam turbine blade and its production method
A steam turbine blade, high temperature technology, applied in the field of mechanical materials, can solve the problems of high temperature lasting low life, mixed crystal structure and other problems
- Summary
- Abstract
- Description
- Claims
- Application Information
AI Technical Summary
Problems solved by technology
Method used
Image
Examples
Embodiment 1
[0028] Prepare high-temperature steam turbine blades according to the following components and methods,
[0029] Step A, carry out vacuum induction smelting according to the composition ratio, in which C element is 0.06%, Cr element is 19.5%, Al element is 1.55%, Ti element is 2.60%, and Ni element balance is carried out at 1470-1500°C. It is 0.5pa, and the refining time is 60min.
[0030] Step B, electroslag remelting is carried out on the electrode rod obtained in step A, the electroslag remelting process controls the melting rate at 4.5kg / min, and the outlet water temperature is 46-52°C;
[0031] Step C, subjecting the steel ingot obtained in step B to high-temperature homogenization treatment, the homogenization treatment temperature is 1120°C, and the heat preservation is ≥ 20h,
[0032] In step D, the temperature of the steel ingot obtained in step C is lowered to 1130° C., and after being kept for 3 hours, cross forging is used at this temperature to form a material. ...
Embodiment 2
[0035] Prepare high-temperature steam turbine blades according to the following components and methods:
[0036] Step A, vacuum induction smelting is carried out according to the composition ratio, in which C element is 0.053%, Cr element is 20.5%, Al element is 1.58%, Ti element is 2.55%, and Ni element balance is carried out at 1470-1500°C for casting electrode rods; vacuum degree 0.5pa, refining time 60min;
[0037] Step B, electroslag remelting is carried out on the electrode rod obtained in step A, the electroslag remelting process controls the melting rate at 4.5kg / min, and the outlet water temperature is 46-52°C;
[0038] Step C, subjecting the steel ingot obtained in step B to high-temperature homogenization treatment, the homogenization treatment temperature is 1120°C, and the heat preservation is ≥ 20h;
[0039] In step D, the temperature of the steel ingot obtained in step C is lowered to 1130° C., and after being kept for 3 hours, the steel ingot obtained in step ...
Embodiment 3
[0042] Prepare high-temperature steam turbine blades according to the following components and methods:
[0043] Step A, vacuum induction smelting is carried out according to the composition ratio, wherein C element is 0.065%, Cr element is 19.5%, Al element is 1.65%, Ti element is 2.60%, and Ni element balance is carried out at 1470-1500°C. It is 0.7pa, and the refining time is 60min.
[0044] In step B, electroslag remelting is performed on the electrode rod obtained in step A, and the electroslag remelting process controls the melting rate at 4.0kg / min, and the outlet water temperature is 46-52°C;
[0045] Step C, subjecting the steel ingot obtained in step B to high-temperature homogenization treatment, the homogenization treatment temperature is 1190-1210°C, and the heat preservation is ≥ 20h;
[0046] In step D, the temperature of the steel ingot obtained in step C is lowered to 1130° C., and after being kept for 3 hours, the steel ingot obtained in step C is formed by cr...
PUM
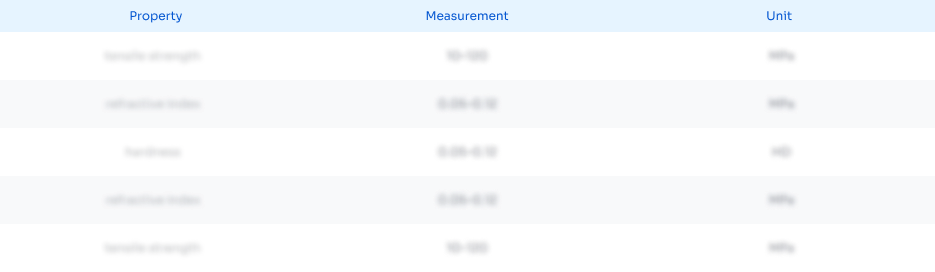
Abstract
Description
Claims
Application Information

- Generate Ideas
- Intellectual Property
- Life Sciences
- Materials
- Tech Scout
- Unparalleled Data Quality
- Higher Quality Content
- 60% Fewer Hallucinations
Browse by: Latest US Patents, China's latest patents, Technical Efficacy Thesaurus, Application Domain, Technology Topic, Popular Technical Reports.
© 2025 PatSnap. All rights reserved.Legal|Privacy policy|Modern Slavery Act Transparency Statement|Sitemap|About US| Contact US: help@patsnap.com