A Process Planning Method for Synchronous Powder Feeding Additive Manufacturing Based on Structural Features
A technology of additive manufacturing and structural features, applied in the field of additive manufacturing, can solve problems such as inability to carry out the process, increase processing procedures, and unstable quality, so as to reduce the difficulty of additive manufacturing process design, improve precision and production efficiency, The effect of shortening the process design cycle
- Summary
- Abstract
- Description
- Claims
- Application Information
AI Technical Summary
Problems solved by technology
Method used
Image
Examples
Embodiment Construction
[0042] The specific implementation manners of the present invention will be further described in detail below in conjunction with the accompanying drawings and embodiments. The following examples are used to illustrate the present invention, but are not intended to limit the scope of the present invention.
[0043] In this embodiment, an aircraft titanium alloy structural part is taken as an example, and the process planning method for synchronous powder feeding additive manufacturing based on structural features of the present invention is used for additive manufacturing.
[0044] A simultaneous powder feeding additive manufacturing process planning method based on structural features, such as figure 1 shown, including the following steps:
[0045] Step 1. Process digital model design: Divide the titanium alloy structural parts into beams, frames, joints, wall panels and ribs, and design the part digital model into a process digital model according to the characteristics of ...
PUM
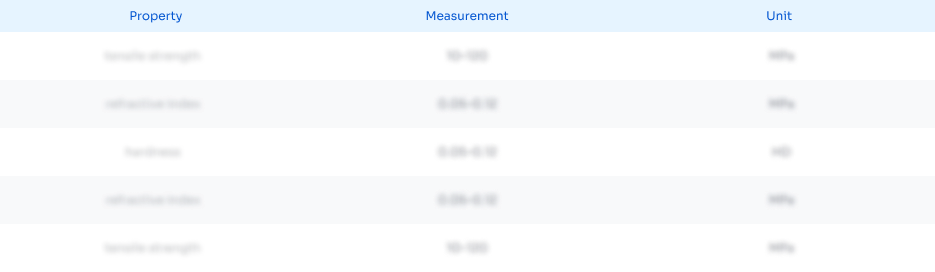
Abstract
Description
Claims
Application Information

- Generate Ideas
- Intellectual Property
- Life Sciences
- Materials
- Tech Scout
- Unparalleled Data Quality
- Higher Quality Content
- 60% Fewer Hallucinations
Browse by: Latest US Patents, China's latest patents, Technical Efficacy Thesaurus, Application Domain, Technology Topic, Popular Technical Reports.
© 2025 PatSnap. All rights reserved.Legal|Privacy policy|Modern Slavery Act Transparency Statement|Sitemap|About US| Contact US: help@patsnap.com