A 5356 aluminum alloy rod continuous casting and rolling production system
A technology of continuous casting and rolling, aluminum alloy rod, applied in the field of 5356 aluminum alloy rod continuous casting and rolling production system, can solve the problem of inability to produce 5356 aluminum alloy rod, and achieve convenient integrated production, high quality and high production efficiency Effect
- Summary
- Abstract
- Description
- Claims
- Application Information
AI Technical Summary
Problems solved by technology
Method used
Image
Examples
Embodiment 1
[0032] A 5356 aluminum alloy rod continuous casting and rolling production system, comprising a melting system 1, a casting machine 2, a rolling pretreatment system 3, a rolling system 4, and a winding system 5 arranged in sequence; the rolling system 4 includes four Rough rolling mills 41 and eight finishing mills 42, four rough rolling mills 41 are arranged near the rolling pretreatment system 3 at the end far away from the eight finishing mills 42, and the end of the eight finishing mills 42 away from the four rough rolling mills 41 is close to the coiling system 5 settings; four rough rolling mills 41 and eight finishing mills 42 are provided with a number of rolls 43, and rolling grooves are arranged on the rolls 43, and the ellipticity of each rolling groove along the moving direction of the 5356 aluminum alloy rod decreases successively, and the adjacent The ellipticity of the rolling groove on the roll 43 of the winding system 5 is zero.
[0033] The SH3200 / 9.5-300 / 4-2...
Embodiment 2
[0038] On the basis of the first embodiment, the diameters of the short sides of the rolling grooves of the rolls 43 on the four roughing mills 41 and the diameters of the short sides of the rolling grooves on the eight finishing mills 42 are both 9.5 mm.
[0039] During the rolling process, the diameter of the short side of the 5356 aluminum alloy rod is always 9.5mm, while the diameter of the long side of the 5356 aluminum alloy rod gradually decreases to ensure that the 5356 aluminum alloy rod can be gradually extended into a cylindrical shape, avoiding the 5356 aluminum alloy rod It is difficult to form when the diameter of the short side and the diameter of the long side of the rod are changed at the same time.
Embodiment 3
[0041] On the basis of Embodiment 1 or Embodiment 2, the casting machine 2 is a four-wheel horizontal casting machine, and the casting machine 2 includes a crystallization wheel, a steel belt, a pressing wheel, a tensioning wheel, a potting device, a cooling device, Spindle picker, approach bridge, oiling device.
[0042] The aluminum alloy liquid can be cast between the crystallization wheel and the steel belt of the four-wheel horizontal casting machine. After casting, the 5356 aluminum alloy rod can be rolled and formed, which is convenient for integrated production.
PUM
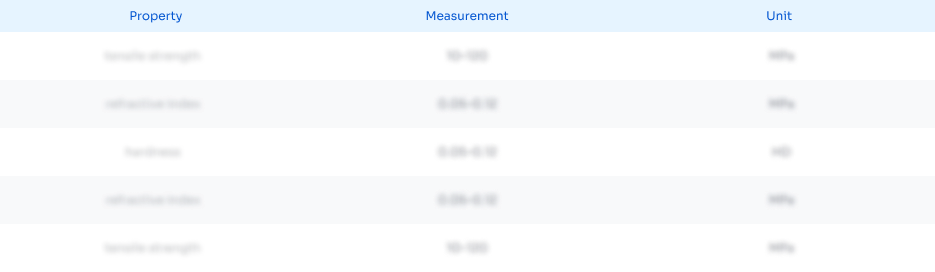
Abstract
Description
Claims
Application Information

- R&D
- Intellectual Property
- Life Sciences
- Materials
- Tech Scout
- Unparalleled Data Quality
- Higher Quality Content
- 60% Fewer Hallucinations
Browse by: Latest US Patents, China's latest patents, Technical Efficacy Thesaurus, Application Domain, Technology Topic, Popular Technical Reports.
© 2025 PatSnap. All rights reserved.Legal|Privacy policy|Modern Slavery Act Transparency Statement|Sitemap|About US| Contact US: help@patsnap.com