A kind of PVC cable material and preparation method thereof
A technology of cable materials and plasticizers, which is applied in circuits, electrical components, plastic/resin/wax insulators, etc., can solve problems such as poor flame retardant effect, increased toxicity index, unsatisfactory flame retardant effect and smoke suppression ability, etc. Achieve good long-term thermal stability, enhanced flame retardant and smoke suppression effects, and good mechanical strength
- Summary
- Abstract
- Description
- Claims
- Application Information
AI Technical Summary
Problems solved by technology
Method used
Examples
Embodiment 1
[0024](1) Preparation of flame retardant: weigh 10 parts of silica and 5 parts of aluminum hydroxide according to the proportions, mix them evenly and put them in a muffle furnace, keep them at 300°C for 2h, then drop to room temperature and put them in a desiccator for use ;
[0025](2) Combine 100 parts of PVC, 50 parts of dioctyl phthalate, 3 parts of liquid calcium zinc stabilizer (calcium: zinc = 2:1), 5 parts of epoxy soybean oil, 30 parts of sodium stearate, 2 parts -Hydroxy-4-methoxybenzophenone 1 part and the flame retardant obtained in step (1) are mixed uniformly, then mixed with a mixer at 170℃~175℃ for 5~10min, and then transferred to the plate for curing On the machine, between 170℃~175℃, under the pressure of 100MPa~120MPa, hot press, take out and then cold press to obtain PVC cable material.
Embodiment 2
[0027](1) Preparation of flame retardant: Weigh 20 parts of silica and 10 parts of aluminum hydroxide according to the proportions, mix them evenly, put them in a muffle furnace, keep the temperature at 300°C for 2h, then lower to room temperature and put them in a desiccator for later use ;
[0028](2) Combine 100 parts of PVC, 50 parts of dibutyl phthalate, 1 part of liquid calcium zinc stabilizer (calcium: zinc = 2:1), 7 parts of epoxy soybean oil, 40 parts of sodium stearate, 2 parts -Hydroxy-4-methoxybenzophenone 1 part and the flame retardant obtained in step (1) are mixed uniformly, then mixed with a mixer at 170℃~175℃ for 5~10min, and then transferred to the plate for curing On the machine, between 170℃~175℃, under the pressure of 100MPa~120MPa, hot press, take out and then cold press to obtain PVC cable material.
Embodiment 3
[0030](1) Preparation of flame retardant: weigh 15 parts of silica and 7.5 parts of aluminum hydroxide according to the proportions, mix them evenly and put them in a muffle furnace, keep them at 300°C for 2h, then cool to room temperature and put them in a desiccator for use ;
[0031](2) Combine 100 parts of PVC, 50 parts of diisobutyl phthalate, 5 parts of liquid calcium zinc stabilizer (calcium: zinc = 2:1), 10 parts of epoxy soybean oil, 50 parts of sodium stearate, After mixing 3 parts of 2-hydroxy-4-methoxybenzophenone with the flame retardant obtained in step (1) uniformly, mix it with a mixer at 170℃~175℃ for 5~10min, then transfer it to the flat plate On the vulcanizing machine, the temperature is between 170°C and 175°C, and the pressure is 100MPa to 120MPa, and then it is taken out and cold pressed to obtain the PVC cable material.
PUM
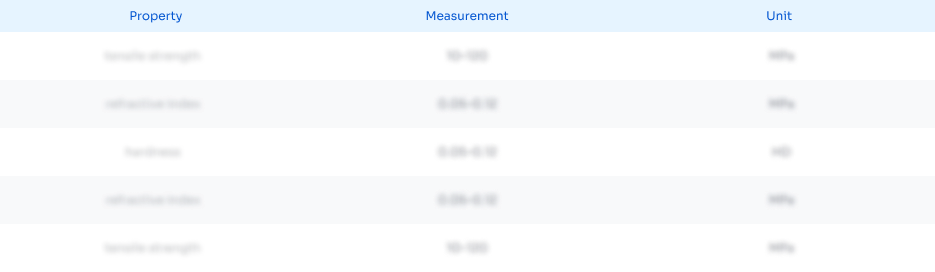
Abstract
Description
Claims
Application Information

- R&D Engineer
- R&D Manager
- IP Professional
- Industry Leading Data Capabilities
- Powerful AI technology
- Patent DNA Extraction
Browse by: Latest US Patents, China's latest patents, Technical Efficacy Thesaurus, Application Domain, Technology Topic, Popular Technical Reports.
© 2024 PatSnap. All rights reserved.Legal|Privacy policy|Modern Slavery Act Transparency Statement|Sitemap|About US| Contact US: help@patsnap.com