Stone coal slag autoclaved brick production method
A production method and a technology of stone coal slag, which are applied in the field of building materials, can solve the problems of the stone coal slag having little use, ecological environment impact, low calorific value, etc., and achieve the effects of considerable economic benefits, simple production process and low cost.
- Summary
- Abstract
- Description
- Claims
- Application Information
AI Technical Summary
Problems solved by technology
Method used
Image
Examples
Embodiment Construction
[0030] The present invention will be further described below in conjunction with the accompanying drawings and specific embodiments.
[0031] In the accompanying drawings, a method for producing autoclaved stone-coal slag bricks, including: limestone, stone coal, clay, vertical lime kiln, lime, lime warehouse, stone coal clay slag, fly ash, pulverizer, digestion A pool, digestion Pool B, digesting pool C, water, brick making machine, green brick car, autoclave, finished brick car, finished brick yard.
[0032] While calcining lime, add 10-20% clay and calcining at the same time, the silicon element and calcium element in stone coal and clay are combined and fired to form a silicate hydraulic substance.
[0033] At the outlet of the vertical kiln, the lime and coal cinder are separated, and the lime is stored in the lime warehouse or loaded on a truck for transportation.
[0034] Among the waste materials, stone coal slag accounts for about 80-85%, clay slag about 10-15%, and ...
PUM
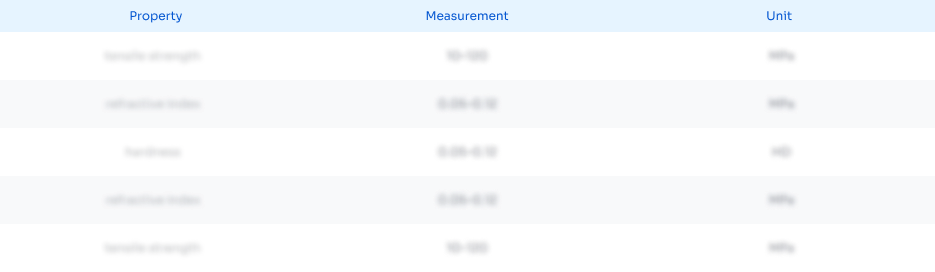
Abstract
Description
Claims
Application Information

- R&D
- Intellectual Property
- Life Sciences
- Materials
- Tech Scout
- Unparalleled Data Quality
- Higher Quality Content
- 60% Fewer Hallucinations
Browse by: Latest US Patents, China's latest patents, Technical Efficacy Thesaurus, Application Domain, Technology Topic, Popular Technical Reports.
© 2025 PatSnap. All rights reserved.Legal|Privacy policy|Modern Slavery Act Transparency Statement|Sitemap|About US| Contact US: help@patsnap.com