Graphene composite rubber for automobile air inlet hose and preparation method thereof
A graphene composite and graphene technology, applied in the field of composite rubber, can solve the problems of immature technology, poor heat resistance and oil resistance, unsatisfactory effect, etc., and achieve the effect of improving heat resistance, oil resistance and preventing further swelling
- Summary
- Abstract
- Description
- Claims
- Application Information
AI Technical Summary
Problems solved by technology
Method used
Image
Examples
Embodiment 1
[0032] a. Add terephthalic acid to ethylene glycol and stir in a water bath at 52°C to form an oil phase liquid;
[0033]b. Add graphene and polyethylene glycol octylphenyl ether into water, ultrasonically disperse for 2.5 hours, add to the oil phase liquid prepared in step a, continue stirring for 30 minutes, add catalyst, heat up to 60°C for reaction, filter, Washing, vacuum drying at 70°C for 24 hours, and further grinding to obtain graphene / polyethylene terephthalate powder microspheres;
[0034] c. Dilute the nitrile rubber to latex with a solid content of 50%, add the powder microspheres prepared in step b into the nitrile latex, stir evenly, use a dilute acid with a mass concentration of 5% for flocculation, and wash at 60°C Down blast drying, obtained graphene / butyronitrile co-precipitation glue;
[0035] d. Put the EPDM rubber into an open mill and plasticize it for 2 minutes, add stearic acid, graphene / nitrile co-precipitation glue, aromatic hydrocarbon oil, acceler...
Embodiment 2
[0039] a. Add terephthalic acid to ethylene glycol and stir in a water bath at 50°C to form an oil phase liquid;
[0040] b. Add graphene and polyethylene glycol octylphenyl ether into water, ultrasonically disperse for 2 hours, add to the oil phase liquid prepared in step a, continue to stir for 20 minutes, add catalyst, heat up to 55°C for reaction, filter and wash , dried in vacuum at 60°C for 26 hours, and further ground to obtain graphene / polyethylene terephthalate powder microspheres;
[0041] c. Dilute the nitrile rubber to latex with a solid content of 40%, add the powder microspheres prepared in step b into the nitrile latex, stir evenly, use a dilute acid with a mass concentration of 5% for flocculation, and wash at 60°C Down blast drying, obtained graphene / butyronitrile co-precipitation glue;
[0042] d. Put EPDM rubber into an open mill to plasticize for 3 minutes, add stearic acid, graphene / nitrile co-precipitation glue, aromatic hydrocarbon oil, accelerator, cro...
Embodiment 3
[0046] a. Add terephthalic acid to ethylene glycol and stir in a water bath at 55°C to form an oil phase liquid;
[0047] b. Add graphene and polyethylene glycol octylphenyl ether into water, ultrasonically disperse for 3 hours, add to the oil phase liquid prepared in step a, continue to stir for 40 minutes, add catalyst, heat up to 65°C for reaction, filter and wash , dried in vacuum at 80°C for 22 hours, and further ground to obtain graphene / polyethylene terephthalate powder microspheres;
[0048] c. Dilute the nitrile rubber into latex with a solid content of 60%, add the powder microspheres prepared in step b into the nitrile latex, stir evenly, use a dilute acid with a mass concentration of 5% for flocculation, and wash at 60°C Down blast drying, obtained graphene / butyronitrile co-precipitation glue;
[0049] d. Put the EPDM rubber into an open mill and plasticize it for 2 minutes, add stearic acid, graphene / nitrile co-precipitation glue, aromatic hydrocarbon oil, accele...
PUM
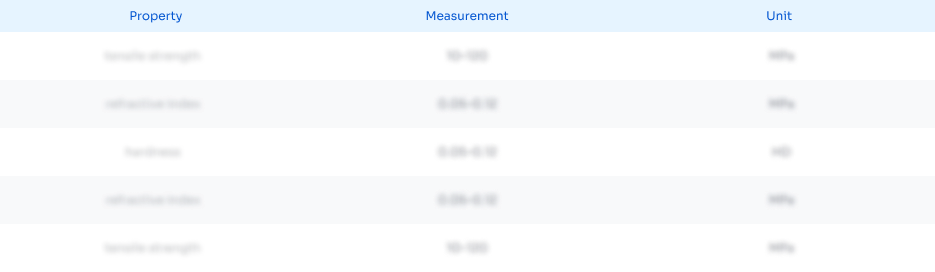
Abstract
Description
Claims
Application Information

- R&D Engineer
- R&D Manager
- IP Professional
- Industry Leading Data Capabilities
- Powerful AI technology
- Patent DNA Extraction
Browse by: Latest US Patents, China's latest patents, Technical Efficacy Thesaurus, Application Domain, Technology Topic, Popular Technical Reports.
© 2024 PatSnap. All rights reserved.Legal|Privacy policy|Modern Slavery Act Transparency Statement|Sitemap|About US| Contact US: help@patsnap.com