A method for preparing battery grade lithium carbonate from waste lithium iron phosphate electrode sheet
A technology of lithium iron phosphate and lithium carbonate, applied in lithium carbonate;/acid carbonate, secondary battery, battery electrode, etc., can solve the waste of lithium element, the purity of lithium carbonate is not high enough, and the leaching rate of lithium element Not high enough to achieve the effect of high recovery rate, simple method and improved leaching rate
- Summary
- Abstract
- Description
- Claims
- Application Information
AI Technical Summary
Problems solved by technology
Method used
Examples
Embodiment 1
[0020] A method for preparing battery-grade lithium carbonate with waste lithium iron phosphate pole piece, comprises the steps:
[0021] Step 1. Weigh 20g of waste lithium iron phosphate pole pieces and release the remaining power;
[0022] Step 2. Put the waste lithium iron phosphate pole pieces that have discharged the electricity in step 1 into a roasting furnace, heat to 800°C, and oxidize and roast for 1 hour, so that the binder and conductive carbon black are burned to obtain lithium iron phosphate Pole piece firing material of active material and current collector aluminum foil;
[0023] Step 3, put the pole piece roasted material obtained in step 2 into a pulverizer and pulverize to obtain a mixed powder of lithium iron phosphate pole piece powder and aluminum powder, and then use a 100-mesh sieve to sieve the mixed powder, and ferric phosphate The lithium pole piece powder is separated from the aluminum powder, and the oversize is aluminum powder, and the undersize ...
Embodiment 2
[0028] Compared with Example 1, the only difference is that the molar ratio Li / H=1.05 of the lithium element in the lithium iron phosphate pole piece powder to the hydrogen element in hydrochloric acid in step 4, the mass solid-liquid ratio of the lithium iron phosphate pole piece powder and hydrochloric acid is 1:2, other conditions are the same as in Example 1.
Embodiment 3
[0030] Compared with Example 1, the only difference is that in step 4, the molar ratio Li / H of the lithium element in the lithium iron phosphate pole piece powder to the hydrogen element in hydrochloric acid is 1.1, and the mass-solid-liquid ratio of the lithium iron phosphate pole piece powder and hydrochloric acid is 1:3, other conditions are the same as in Example 1.
PUM
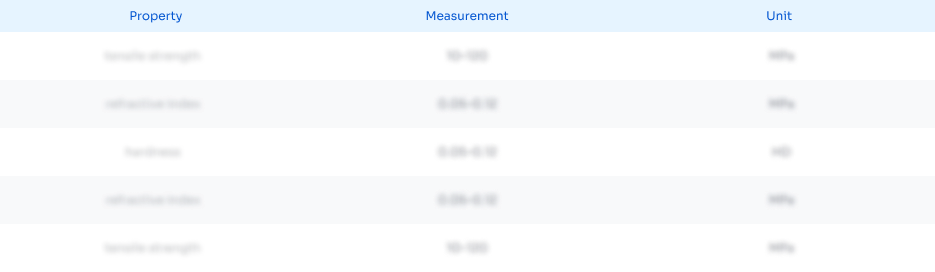
Abstract
Description
Claims
Application Information

- R&D
- Intellectual Property
- Life Sciences
- Materials
- Tech Scout
- Unparalleled Data Quality
- Higher Quality Content
- 60% Fewer Hallucinations
Browse by: Latest US Patents, China's latest patents, Technical Efficacy Thesaurus, Application Domain, Technology Topic, Popular Technical Reports.
© 2025 PatSnap. All rights reserved.Legal|Privacy policy|Modern Slavery Act Transparency Statement|Sitemap|About US| Contact US: help@patsnap.com