Method for recycling zinc and iron in zinc oxygen pressure leaching slag
A technology for leaching slag and zinc oxide, which is applied in the direction of improving process efficiency, can solve the problems of no fixed process route, complex impurity content and types, and large differences in the properties of zinc-oxygen pressure leaching slag, achieving huge environmental benefits and economic benefits Benefits, low cost, and no pollution to the environment
- Summary
- Abstract
- Description
- Claims
- Application Information
AI Technical Summary
Problems solved by technology
Method used
Image
Examples
Embodiment 1
[0031] process such as figure 1 As shown, 100g of a zinc oxygen pressure leaching residue (Zn 5.78%, Fe 20.01%) was ground to a particle size of -200 mesh to -400 mesh, mixed with 60g of concentrated sulfuric acid (content 98%), and 10g of magnesium hydrogen sulfate. Mix evenly, put it into a muffle furnace for roasting, control the roasting temperature to 250° C., and roast for 2 hours. After the calcination, the calcined sand obtained was added to the sulfuric acid solution (concentration ~ 1wt%), the solid-to-liquid ratio (g / mL) was 1:5, stirred at 50° C. for 1 h, and then filtered to obtain the zinc-containing iron filtrate I and Leach residue. Add reduced iron powder to the zinc-containing iron filtrate I, the added amount is 1.1 times of the theoretical amount, the reduction time is 0.5h, and then filter to obtain the zinc-containing iron filtrate II and iron powder reduction slag. Carry out the extraction of zinc to zinc-containing iron filtrate II, extractant is P204...
Embodiment 2
[0034] process such as figure 1 As shown, 100g of a zinc oxygen pressure leaching residue (Zn 5.78%, Fe 20.01%) was ground to a particle size of -200 mesh to -400 mesh, mixed with concentrated sulfuric acid (content 98%) 80g, potassium hydrogensulfate 30g and Mix evenly, put it into a muffle furnace for roasting, control the roasting temperature to 300° C., and roast for 3 hours. After the roasting, the calcined sand obtained was added to the sulfuric acid solution (concentration ~ 2wt%), the solid-to-liquid ratio (g / mL) was 1:5, stirred at 70° C. for 1 h, and then filtered to obtain the zinc-containing iron filtrate I and Leach residue. Add reduced iron powder to the zinc-containing iron filtrate I, the addition amount is 1.1 times of the theoretical amount, and the reduction time is 1 hour, and then filter to obtain the zinc-containing iron filtrate II and iron powder reduction slag. The zinc-containing iron filtrate II is carried out to the extraction of zinc, the extract...
Embodiment 3
[0037] process such as figure 1 As shown, 100g of a zinc oxygen pressure leaching residue (Zn 5.78%, Fe 20.01%) was ground to a particle size of -200 mesh to -400 mesh, mixed with concentrated sulfuric acid (content 98%) 90g, ammonium bisulfate 40g and Mix evenly, put it into a muffle furnace for roasting, control the roasting temperature to 300° C., and the roasting time to be 3.5 hours. After the roasting, the calcined sand obtained was added to the sulfuric acid solution (concentration ~ 4wt%), the solid-to-liquid ratio (g / mL) was 1:5, stirred at 80° C. for 1 h, and then filtered to obtain the zinc-containing iron filtrate I and Leach residue. Add reduced iron powder to the zinc-containing iron filtrate I, the addition amount is 1.2 times of the theoretical amount, and the reduction time is 1 h, and then filter to obtain the zinc-containing iron filtrate II and iron powder reduction slag. The zinc-containing iron filtrate II is carried out to the extraction of zinc, the e...
PUM
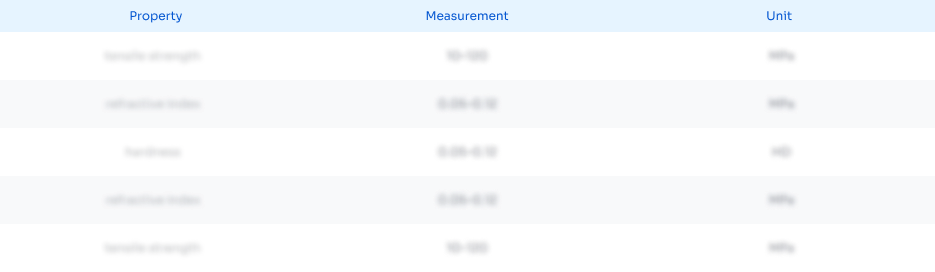
Abstract
Description
Claims
Application Information

- Generate Ideas
- Intellectual Property
- Life Sciences
- Materials
- Tech Scout
- Unparalleled Data Quality
- Higher Quality Content
- 60% Fewer Hallucinations
Browse by: Latest US Patents, China's latest patents, Technical Efficacy Thesaurus, Application Domain, Technology Topic, Popular Technical Reports.
© 2025 PatSnap. All rights reserved.Legal|Privacy policy|Modern Slavery Act Transparency Statement|Sitemap|About US| Contact US: help@patsnap.com