High-end grinding technology equipment
A kind of process equipment and high-end technology, applied in the field of high-end grinding process equipment, can solve the problems of low degree of automation, high labor intensity, low work efficiency, etc., and achieve the effect of high degree of automation, reduce labor intensity and improve work efficiency
- Summary
- Abstract
- Description
- Claims
- Application Information
AI Technical Summary
Problems solved by technology
Method used
Image
Examples
Embodiment Construction
[0019] Such as Figure 1-2 As shown, a high-end grinding process equipment of the present invention includes a base 10, a support column 11 fixedly arranged above the base 10, and a rotary sleeve 12 arranged on the left end surface of the support column 11. The rotary sleeve 12 is provided with a first rotary cavity 34 that is symmetrical up and down and with ports facing outwards. In the first rotary cavity 34, a rotary plate 37 is rotatably provided through the first rotary shaft 46. The outer end surface of the rotary plate 37 is fixed with a grinding wheel. Strip 36, the inner end surface of the rotating plate 37 is fixed with a cleaning cotton 39, and the left end surface of the rotating plate 37 is symmetrically provided with a locking hole 35 with the port facing left. In the left inner wall of the first rotating cavity 34 A first sliding groove 33 opposite to the locking hole 35 is symmetrically arranged up and down, and a locking block 32 is slidably installed in the ...
PUM
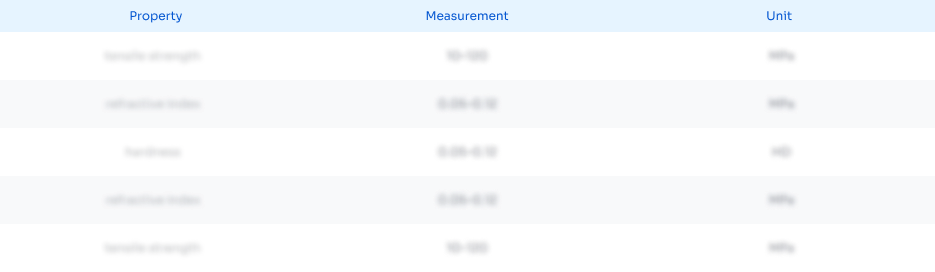
Abstract
Description
Claims
Application Information

- R&D Engineer
- R&D Manager
- IP Professional
- Industry Leading Data Capabilities
- Powerful AI technology
- Patent DNA Extraction
Browse by: Latest US Patents, China's latest patents, Technical Efficacy Thesaurus, Application Domain, Technology Topic, Popular Technical Reports.
© 2024 PatSnap. All rights reserved.Legal|Privacy policy|Modern Slavery Act Transparency Statement|Sitemap|About US| Contact US: help@patsnap.com