Reduction and passivation method of copper-based catalyst for hydrogen production from methanol reforming
A copper-based catalyst, reforming hydrogen production technology, applied in catalyst activation/preparation, chemical instruments and methods, physical/chemical process catalysts, etc., can solve the special requirements of passivation gas space velocity, complex process and investment cost Large and other problems, to achieve the effect of saving N2 consumption, convenient temperature control operation, and solving the difficulty of temperature control
- Summary
- Abstract
- Description
- Claims
- Application Information
AI Technical Summary
Problems solved by technology
Method used
Image
Examples
Embodiment 1
[0030] A reduction method of a copper-based catalyst for producing hydrogen by methanol reforming, specifically comprising the following steps:
[0031] (1) Air heating process: the heat transfer oil is used as the heating source, and the air is used as the heat carrier. -1 ; The temperature rises at a rate of 20°C / h, and the catalyst bed in the converter needs to be heated to 120°C for 3 to 5 hours at a constant temperature. At this time, the catalyst will release adsorbed physical water; after the constant temperature is over, continue to heat the catalyst bed in the converter to 160°C. ℃, constant temperature for 2~3h, to ensure that the temperature difference of the catalyst bed is within 5℃; when the temperature of the catalyst bed in the converter reaches the specified temperature, the air passes through the vaporization superheater, the converter, the heat exchanger, the water cooler, and the water washing tower in turn. , and discharge after the water separator.
[00...
Embodiment 2
[0037] A reduction method of a copper-based catalyst for producing hydrogen by methanol reforming, specifically comprising the following steps:
[0038](1) Air heating process: heat transfer oil is used as the heating source, air is used as the heat carrier, and the air is distributed into the system from the shower nozzle at the bottom of the vaporization superheater, and the heating space speed is 300h -1 ;Raise the temperature at a rate of 25°C / h. After the temperature of the catalyst bed in the converter is raised to 120°C, the temperature needs to be kept constant for 3 to 5 hours. At this time, the catalyst will release adsorbed physical water; ℃, constant temperature for 2 to 3 hours, to ensure that the temperature difference of the catalyst bed is within 5°C; when the temperature of the catalyst bed in the converter reaches the specified temperature, the air passes through the vaporization superheater, the converter, the heat exchanger, the water cooler, and the water w...
Embodiment 3
[0044] A method for reducing a copper-based catalyst for methanol reforming hydrogen production, specifically comprising the following steps:
[0045] (1) Air heating process: heat transfer oil is used as the heating source, air is used as the heat carrier, and the air is distributed into the system from the shower nozzle at the bottom of the vaporization superheater, and the heating space speed is 450h -1 It is advisable to raise the temperature at a rate of 30°C / h. After the temperature of the catalyst bed in the converter is raised to 120°C, the temperature needs to be kept constant for 3 to 5 hours. At this time, the catalyst will release adsorbed physical water; to 160°C, keep the temperature constant for 2 to 3 hours, and ensure that the temperature difference of the catalyst bed is within 5°C; It is discharged from the water washing tower and water separator.
[0046] (2) Steam heating process: After the constant temperature is over and the temperature difference of th...
PUM
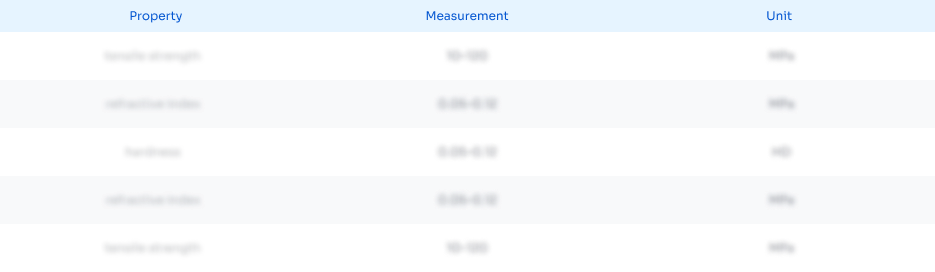
Abstract
Description
Claims
Application Information

- Generate Ideas
- Intellectual Property
- Life Sciences
- Materials
- Tech Scout
- Unparalleled Data Quality
- Higher Quality Content
- 60% Fewer Hallucinations
Browse by: Latest US Patents, China's latest patents, Technical Efficacy Thesaurus, Application Domain, Technology Topic, Popular Technical Reports.
© 2025 PatSnap. All rights reserved.Legal|Privacy policy|Modern Slavery Act Transparency Statement|Sitemap|About US| Contact US: help@patsnap.com