Turbulence structure for array impact jet cooling
A technology of impinging jets and arrays, which is applied in the field of spoiler structures, can solve problems such as large temperature gradients, offsets, and unreasonable impingement cooling systems, and achieve the effects of improving heat transfer efficiency, increasing heat transfer efficiency, and uniform temperature distribution
- Summary
- Abstract
- Description
- Claims
- Application Information
AI Technical Summary
Problems solved by technology
Method used
Image
Examples
Embodiment Construction
[0031] The invention will be described in further detail below in conjunction with the accompanying drawings and specific examples, but the present invention is not limited to the following examples.
[0032] refer to figure 1 , a high-performance turbulence structure in array impingement jet cooling, comprising a jet orifice 1 and a jet target 3, the jet orifice 1 is provided with a plurality of impingement holes 2 arranged in an array; the jet orifice 1 is located in the The upper part of the jet target plate 3 is designed as a cavity between the two, and the spoiler column 4 is arranged on the jet target plate 3 , and the upper end of the spoiler column 4 is in contact with the jet orifice plate 1 . In this solution, the diameter of the impact hole 2 is set as D.
[0033] The spoiler column 4 is a column with a different pentagonal section, or a column with a nearly semi-elliptical dome-shaped section, or a column with a drop-shaped section.
[0034] As a scheme improveme...
PUM
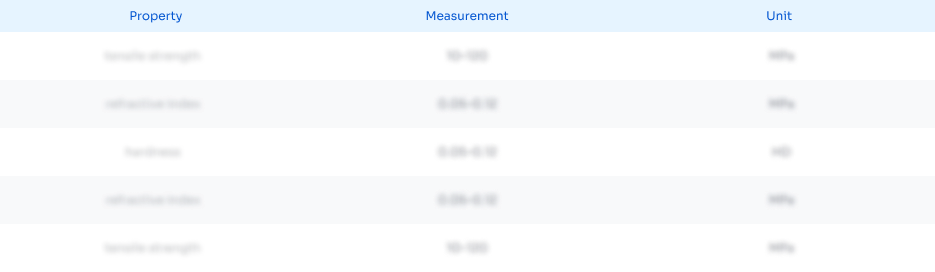
Abstract
Description
Claims
Application Information

- R&D
- Intellectual Property
- Life Sciences
- Materials
- Tech Scout
- Unparalleled Data Quality
- Higher Quality Content
- 60% Fewer Hallucinations
Browse by: Latest US Patents, China's latest patents, Technical Efficacy Thesaurus, Application Domain, Technology Topic, Popular Technical Reports.
© 2025 PatSnap. All rights reserved.Legal|Privacy policy|Modern Slavery Act Transparency Statement|Sitemap|About US| Contact US: help@patsnap.com