Preparation method of carbon nanotube-carbon fiber mixed enhanced epoxy resin composite material
A carbon nanotube and epoxy resin technology, which is applied in the field of preparation of carbon nanotube-carbon fiber hybrid reinforced epoxy resin composite materials, can solve problems such as the reduction of fiber mechanical properties, achieve performance improvement, increase shear strength, and improve infiltration. sexual effect
- Summary
- Abstract
- Description
- Claims
- Application Information
AI Technical Summary
Problems solved by technology
Method used
Image
Examples
Embodiment 1
[0028] The preparation method of the carbon nanotube-carbon fiber hybrid reinforced epoxy resin composite material provided in this embodiment includes the following steps in order:
[0029] (1) Modification of carbon fiber surface:
[0030] The commercially available industrial grade JT300A carbon fiber was immersed in analytically pure ammonia water, etched at 25°C for 12 hours, and then the carbon fiber was washed with deionized water several times to remove residual ammonia water on the surface; the carbon fiber treated with ammonia water Immerse in concentrated nitric acid of analytical grade, oxidize at 115°C for 5 minutes at a constant temperature, and then wash the carbon fiber with deionized water several times to remove residual nitric acid on the surface; finally put it in a vacuum drying oven and dry it at a drying temperature of 100°C Vacuum dried for 3 hours for later use.
[0031] (2) prepare the sizing agent containing carbon nanotubes:
[0032] Add 20g of TG...
Embodiment 2
[0040] The preparation method of the carbon nanotube-carbon fiber hybrid reinforced epoxy resin composite material provided in this embodiment includes the following steps in order:
[0041] (1) Modification of carbon fiber surface:
[0042] Commercially available industrial grade JT300A carbon fibers were immersed in analytically pure ammonia water, etched at 25°C for 24 hours, and then the carbon fibers were washed with deionized water for several times to remove residual ammonia water on the surface; the carbon fibers treated with ammonia water Immerse in concentrated nitric acid of analytical grade, oxidize at a constant temperature of 115°C for 10 minutes, then wash the carbon fiber with deionized water several times to remove residual nitric acid on the surface; Vacuum dried for 3h for later use.
[0043] (2) prepare the sizing agent containing carbon nanotubes:
[0044] Add 20g of TGDDM resin, 1.0g of carboxylated multi-walled carbon nanotubes with a diameter of 40-60...
PUM
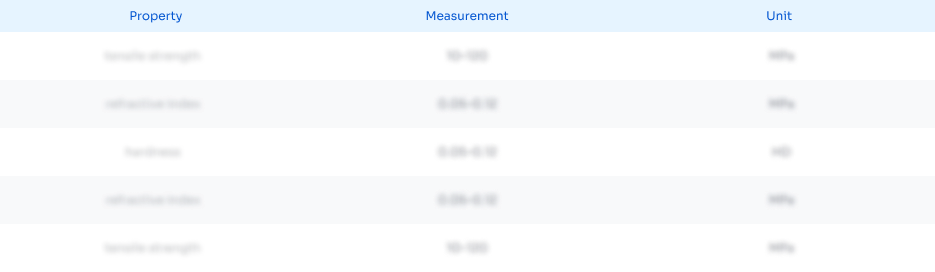
Abstract
Description
Claims
Application Information

- R&D Engineer
- R&D Manager
- IP Professional
- Industry Leading Data Capabilities
- Powerful AI technology
- Patent DNA Extraction
Browse by: Latest US Patents, China's latest patents, Technical Efficacy Thesaurus, Application Domain, Technology Topic, Popular Technical Reports.
© 2024 PatSnap. All rights reserved.Legal|Privacy policy|Modern Slavery Act Transparency Statement|Sitemap|About US| Contact US: help@patsnap.com