Photo-thermal dual-curing plastic coating
A dual-curing, plastic coating technology, used in polyester coatings, epoxy resin coatings, polyurea/polyurethane coatings, etc., can solve problems such as difficult curing, poor film performance, and easy shading of light, reducing production. Cost, good performance, and the effect of simplifying the spraying process
- Summary
- Abstract
- Description
- Claims
- Application Information
AI Technical Summary
Problems solved by technology
Method used
Examples
Embodiment 1
[0023] Components and proportioning amount (parts by weight) are as follows:
[0024] A component: EBECRYL8210 (cytec) 26, isobornyl acrylate 2, 1,6-hexanediol diacrylate 4, ethoxylated trimethylolpropane triacrylate 2, dipentaerythritol pentaacrylate 4, CN2252 ( Sartomer) 3, CN104 (Sartomer) 2, EBECRYL5129 (Cytec) 2, CN9010 (Sartomer) 6, organic pigment 3, additive 3, 2,4,6-trimethylbenzoyl di Phenylphosphine oxide 2, solvent 41.
[0025] B component: toluene diisocyanate 50, solvent 50.
[0026] Production Method:
[0027] a. Configuration of component A: Accurately weigh each component according to the proportion of the formula and add them to the mixing vessel in turn. Stir fully for 2 hours in a dust-free and light-proof environment. After passing through a 100-mesh filter, the filtrate can be packaged and stored.
[0028] b. Configuration of component B: Accurately weigh each component according to the proportion of the formula and add them to the mixing vessel in tur...
Embodiment 2
[0031] Components and proportioning amount (parts by weight) are as follows:
[0032] Component A: EBECRYL8210 (Cytec) 20, SB404 (Sartomer) 6, Tripropylene Glycol Diacrylate 4, Diethylene Glycol Methyl Diacrylate 4, Trimethylolpropane Triacrylate 2, Dipentaerythritol Hexa Acrylate 4, EBECRYL402 (Cytec) 1, EBECRYL4858 (Cytec) 3, CN9276 (Sartomer) 4, EBECRYL5129 (Cytec) 5, Organic Pigment 5, Additive 4, 1-Hydroxy-Cyclohexyl-Benzene Methyl ketone 3, solvent 35.
[0033] B component: toluene diisocyanate 55, solvent 45.
[0034] The manufacturing method and construction process of this embodiment are the same as those of Example 1, and the performance indicators are shown in Table 1.
Embodiment 3
[0036] Components and proportioning amount (parts by weight) are as follows:
[0037] Component A: lauric acid acrylate 2, neopentyl glycol diacrylate 6, trimethylolpropane triacrylate 2, dipentaerythritol pentaacrylate 4, EBECRYL4858 (Cytec) 3, CN118 (Sartomer) 2 , EBECRYL205 (Cytec) 4, CN2250 (Sartomer) 4, EBECRYL8210 (Cytec) 18, SB405 (Sartomer) 10, organic pigment 5, additive 3, 2-hydroxy-2-methyl-1- Phenyl-1-propanone 3, solvent 34.
[0038] B component: toluene diisocyanate 60, solvent 40.
[0039] The manufacturing method and construction process of this embodiment are the same as those of Example 1, and the performance indicators are shown in Table 1.
PUM
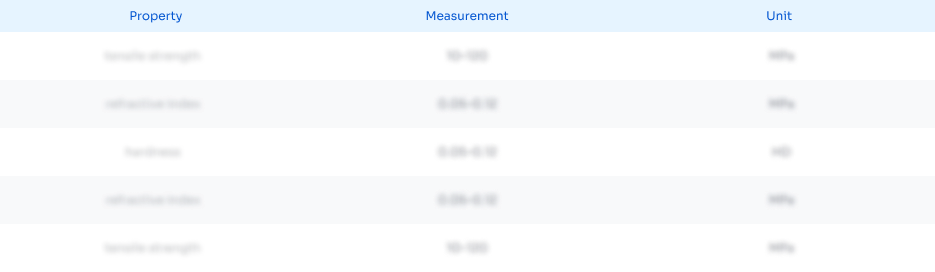
Abstract
Description
Claims
Application Information

- R&D
- Intellectual Property
- Life Sciences
- Materials
- Tech Scout
- Unparalleled Data Quality
- Higher Quality Content
- 60% Fewer Hallucinations
Browse by: Latest US Patents, China's latest patents, Technical Efficacy Thesaurus, Application Domain, Technology Topic, Popular Technical Reports.
© 2025 PatSnap. All rights reserved.Legal|Privacy policy|Modern Slavery Act Transparency Statement|Sitemap|About US| Contact US: help@patsnap.com